Introduction: Navigating the Global Market for rgb led strip connector
The global demand for RGB LED strip connectors continues to surge as businesses across Africa, South America, the Middle East, and Europe seek efficient, reliable solutions for dynamic lighting applications. These connectors are essential components that ensure seamless electrical and signal continuity between LED strip segments, directly impacting installation quality, system longevity, and overall lighting performance. For international B2B buyers, understanding the nuances of RGB LED strip connectors is critical to sourcing products that meet rigorous operational standards and diverse environmental conditions.
This guide offers a comprehensive overview tailored to empower procurement professionals, electrical contractors, and facility managers with actionable insights. You will explore the various types of connectors—including waterproof and non-waterproof options—alongside an examination of materials that affect durability and conductivity. The guide also covers manufacturing standards and quality control processes, helping you identify suppliers who consistently deliver products that comply with international safety and performance benchmarks.
Additionally, you will gain clarity on cost factors and market trends, enabling you to balance budget constraints with quality requirements in regions with varying infrastructure and climate challenges. This resource addresses frequent questions related to installation compatibility, voltage requirements, and connector longevity, ensuring you make informed sourcing decisions that reduce maintenance costs and optimize system reliability.
By leveraging this guide, B2B buyers from emerging and established markets such as Turkey, Indonesia, Brazil, South Africa, and the UAE can confidently navigate the complexities of the global RGB LED strip connector market and secure partnerships that drive successful lighting projects worldwide.
Understanding rgb led strip connector Types and Variations
Type Name | Key Distinguishing Features | Primary B2B Applications | Brief Pros & Cons for Buyers |
---|---|---|---|
Snap-On Connectors | Tool-free, clip-on design for quick ribbon-to-ribbon joining | Retail lighting, event setups, short runs | Pros: Easy installation, no soldering; Cons: Limited durability under harsh conditions |
Ribbon-to-Wire Connectors | Converts strip terminals to wire leads for flexible wiring | Custom installations, complex layouts | Pros: Versatile wiring options; Cons: Slightly higher cost and complexity |
Waterproof Connectors | Sealed connectors with IP65+ rating for outdoor/wet areas | Outdoor signage, architectural lighting | Pros: Weather resistance; Cons: Bulkier size, higher price |
Soldered Connectors | Permanent joint requiring soldering for secure connections | Long-term industrial installations | Pros: Highest reliability and conductivity; Cons: Requires skilled labor, time-consuming |
Terminal Block Connectors | Screw-tightened wire clamps for robust mechanical connection | High-current commercial LED systems | Pros: Strong mechanical hold, reusable; Cons: Larger footprint, more complex assembly |
Snap-On Connectors are widely favored for their simplicity and speed, ideal for retail or event lighting where installations are temporary or frequently adjusted. They eliminate the need for soldering, reducing labor costs and training requirements. However, buyers should consider their limited mechanical strength and suitability mainly for indoor, low-stress environments.
Ribbon-to-Wire Connectors provide flexibility by enabling LED strips to connect directly to wire harnesses. This type is essential for complex commercial layouts or installations requiring precise routing around obstacles. The slightly increased cost and need for careful planning are offset by enhanced adaptability and cleaner wiring aesthetics, critical in professional-grade projects.
Waterproof Connectors are indispensable for outdoor or moisture-prone environments, offering robust protection against dust and water ingress. These connectors comply with IP65 or higher standards, making them suitable for architectural lighting, outdoor signage, and harsh climate zones such as parts of Africa and the Middle East. Buyers should be mindful of their larger size and higher price point but gain long-term durability and reduced maintenance.
Soldered Connectors represent the gold standard for permanent, high-reliability connections, especially in industrial or large-scale commercial applications. While requiring skilled labor and longer installation times, they offer superior electrical performance and mechanical stability. International buyers investing in long-term infrastructure projects often prefer this method for its proven longevity and minimal failure rates.
Terminal Block Connectors use screw clamps to secure wires mechanically and are favored in high-current or modular commercial LED systems. Their reusable nature and strong hold make them suitable for installations requiring periodic maintenance or upgrades. The trade-off includes a larger physical footprint and more intricate assembly, factors buyers must weigh against installation environment constraints and system complexity.
Related Video: 5 Different Ways to connect your RGB Light Strip (NO SOLDERING)
Key Industrial Applications of rgb led strip connector
Industry/Sector | Specific Application of rgb led strip connector | Value/Benefit for the Business | Key Sourcing Considerations for this Application |
---|---|---|---|
Retail & Commercial Spaces | Dynamic lighting installations for storefronts and displays | Enhances visual appeal, attracts customers, and drives sales | Durable, easy-to-install connectors with consistent color control; waterproof options for outdoor displays |
Hospitality & Entertainment | Ambient and accent lighting in hotels, restaurants, and theaters | Creates immersive environments, improves guest experience | Flexible connectors compatible with various LED strip types; compliance with local electrical standards |
Automotive & Transportation | Interior and exterior decorative lighting for vehicles | Customizable lighting solutions that increase product appeal | High-temperature resistant connectors; vibration-proof and secure locking mechanisms |
Architectural & Urban Lighting | Façade lighting and public space illumination | Energy-efficient, customizable lighting enhances aesthetics | Weatherproof and corrosion-resistant connectors; long cable runs compatibility for large installations |
Manufacturing & Warehousing | Task and safety lighting in production lines and storage areas | Improves worker safety and operational efficiency | Robust connectors with high current capacity; easy maintenance and replacement features |
In the retail and commercial sector, rgb led strip connectors are essential for creating vibrant, eye-catching lighting displays. These connectors enable seamless installation and maintenance of dynamic RGB LED strips used in storefront windows and interior merchandising displays. For international buyers, especially in regions like Africa and South America, sourcing connectors that offer waterproofing and robust color consistency is critical due to varying climate conditions and the need for reliable outdoor installations.
Within the hospitality and entertainment industry, rgb led strip connectors facilitate the deployment of ambient and accent lighting that enhances guest experiences in hotels, restaurants, and theaters. These connectors must be flexible enough to accommodate different LED strip types and comply with diverse electrical codes across Europe and the Middle East. Buyers should prioritize connectors that support dimming and color control features to create customizable atmospheres that meet high aesthetic standards.
In the automotive and transportation sector, rgb led strip connectors are used to implement customizable interior and exterior vehicle lighting. Connectors here must withstand harsh conditions such as temperature extremes and vibration, which are common in vehicle applications. International B2B buyers from regions with hot climates, like the Middle East or Indonesia, should focus on sourcing connectors with high-temperature tolerance and secure locking mechanisms to ensure durability and safety.
For architectural and urban lighting projects, rgb led strip connectors enable large-scale façade illumination and public space lighting. These applications require connectors that are weatherproof, corrosion-resistant, and capable of supporting long cable runs without significant voltage drop. Buyers from Europe and coastal regions in South America should consider connectors designed for outdoor use with IP65 or higher ratings to ensure longevity and consistent performance.
Finally, in manufacturing and warehousing environments, rgb led strip connectors support task and safety lighting installations that improve operational efficiency and worker safety. Connectors used here must handle higher current loads and allow for quick maintenance or replacement to minimize downtime. International buyers should seek connectors with robust construction and compatibility with industrial wiring standards to meet the demanding conditions of these sectors.
Related Video: How To Set Up Govee RGB LED Strip Lights With Corners Angles And More Tips
Strategic Material Selection Guide for rgb led strip connector
When selecting materials for RGB LED strip connectors, international B2B buyers must carefully evaluate the physical, electrical, and environmental properties of each option. The choice of connector material directly influences product reliability, installation ease, and compatibility with diverse operating environments typical in Africa, South America, the Middle East, and Europe. Below is an in-depth analysis of four common materials used in RGB LED strip connectors.
1. Polycarbonate (PC)
Key Properties:
Polycarbonate is a durable thermoplastic known for its excellent impact resistance, high temperature tolerance (typically up to 120°C), and good electrical insulation properties. It also offers moderate chemical resistance and UV stability, which is essential for outdoor or semi-exposed installations.
Pros & Cons:
Polycarbonate connectors are lightweight, cost-effective, and easy to manufacture with injection molding, enabling complex shapes and tight tolerances. However, PC can degrade under prolonged exposure to harsh UV radiation unless specially treated, and it is less resistant to certain solvents and chemicals compared to some engineering plastics.
Impact on Application:
PC connectors are ideal for indoor and sheltered outdoor RGB LED strip installations where moderate mechanical strength and electrical insulation are required. They perform well in commercial lighting projects across temperate climates but may need UV-stabilized grades for Middle Eastern or African outdoor applications.
Considerations for International Buyers:
Buyers in regions with high UV exposure or chemical pollutants should specify UV-resistant or flame-retardant PC grades compliant with international standards like UL 94 V-0 or IEC 60695. European and Turkish markets often demand RoHS and REACH compliance for plastics, while buyers in South America and Africa should verify local fire safety certifications.
2. Polyvinyl Chloride (PVC)
Key Properties:
PVC is a widely used plastic with good flexibility, electrical insulation, and chemical resistance. It withstands temperatures up to about 70-80°C and exhibits good resistance to moisture and many acids and alkalis.
Pros & Cons:
PVC connectors are inexpensive and easy to produce, making them attractive for budget-conscious projects. Their flexibility aids in installation where connectors must bend or flex. However, PVC has lower heat resistance and mechanical strength compared to PC or engineering plastics, and it can emit harmful fumes if burned.
Impact on Application:
PVC connectors suit indoor RGB LED strip installations with moderate environmental demands. They are less suitable for high-temperature or outdoor applications, especially in hot climates like parts of Africa or the Middle East, where heat degradation risks increase.
Considerations for International Buyers:
Buyers should ensure PVC materials meet local environmental and safety regulations, such as halogen-free requirements in Europe or specific fire retardancy standards in South America. PVC connectors should be avoided in projects requiring long-term outdoor exposure or high-temperature resistance.
3. Nylon (Polyamide)
Key Properties:
Nylon is a robust engineering plastic with excellent mechanical strength, abrasion resistance, and good chemical resistance. It typically withstands temperatures up to 150°C and offers good electrical insulation. Nylon also has inherent flame retardant properties.
Pros & Cons:
Nylon connectors provide superior durability and longevity, suitable for demanding industrial environments. They resist cracking and deformation under stress, making them ideal for connectors subject to mechanical strain. On the downside, nylon can absorb moisture, which may affect dimensional stability and electrical properties if not properly treated.
Impact on Application:
Nylon is preferred for RGB LED strip connectors in harsh or outdoor environments, including industrial facilities and commercial installations in regions with extreme temperature fluctuations, such as parts of Europe and the Middle East. Its chemical resistance also suits applications exposed to cleaning agents or pollutants.
Considerations for International Buyers:
Buyers should specify moisture-resistant or glass-filled nylon grades for humid climates like Southeast Asia or coastal South America. Compliance with ASTM D4066 (Nylon classification) and IEC 60695 (flammability) standards is critical for ensuring quality and safety. Nylon connectors generally command a higher price but offer excellent lifecycle value.
4. Silicone Rubber (for Sealing Components)
Key Properties:
Silicone rubber is a flexible, high-temperature resistant elastomer with excellent weathering, UV, and chemical resistance. It can operate in temperatures ranging from -60°C to +230°C and maintains elasticity over time.
Pros & Cons:
Silicone is primarily used for waterproofing seals and gaskets in RGB LED strip connectors rather than the connector body itself. It provides superior sealing against moisture and dust ingress, critical for outdoor or wet environment installations. However, silicone is more expensive and less mechanically rigid, so it is combined with harder plastics.
Impact on Application:
Silicone seals are essential for connectors used in outdoor lighting projects in Africa, the Middle East, and coastal regions of South America and Europe where waterproofing (IP65 or higher) is mandatory. They enhance connector longevity by preventing corrosion and electrical shorts.
Considerations for International Buyers:
Buyers should verify that silicone components meet IP rating requirements and international standards such as IEC 60529. In markets with heavy rainfall or dust (e.g., Middle East deserts, tropical South America), silicone-sealed connectors provide a competitive advantage. Cost considerations must balance performance needs.
Summary Table of RGB LED Strip Connector Materials
Material | Typical Use Case for rgb led strip connector | Key Advantage | Key Disadvantage/Limitation | Relative Cost (Low/Med/High) |
---|---|---|---|---|
Polycarbonate | Indoor and sheltered outdoor connectors | High impact resistance, good electrical insulation | UV degradation risk without treatment | Medium |
PVC | Budget indoor connectors with moderate environmental demands | Low cost, flexible for easy installation | Low heat resistance, poor outdoor durability | Low |
Nylon | Industrial and harsh environment connectors | Excellent mechanical strength and chemical resistance | Moisture absorption affecting stability | High |
Silicone Rubber | Waterproof sealing components in outdoor/wet environments | Superior weatherproofing and elasticity | Higher cost, not structurally rigid | High |
This guide empowers international B2B buyers to make informed decisions tailored to their region’s environmental conditions, regulatory requirements, and project budgets. Selecting the right material for RGB LED strip connectors ensures enhanced product performance, durability, and customer satisfaction across diverse markets.
In-depth Look: Manufacturing Processes and Quality Assurance for rgb led strip connector
The manufacturing and quality assurance of RGB LED strip connectors are critical components in ensuring reliable, durable, and high-performance lighting solutions for international B2B buyers. Understanding the production workflow and quality controls helps buyers from regions such as Africa, South America, the Middle East, and Europe make informed supplier selections and manage supply chain risks effectively.
Manufacturing Processes of RGB LED Strip Connectors
The production of RGB LED strip connectors typically follows a structured multi-stage process designed to optimize electrical performance, mechanical integrity, and user-friendly installation.
1. Material Preparation
- Raw Materials: High-quality copper alloys are used for conductive parts due to their excellent electrical conductivity and corrosion resistance. Plastic components often utilize flame-retardant, UV-resistant polymers such as polycarbonate (PC) or acrylonitrile butadiene styrene (ABS).
- Component Sourcing: For B2B buyers, verifying that suppliers source materials from certified vendors can ensure consistency and compliance with international standards.
- Pre-treatment: Metal parts may undergo cleaning and plating processes (e.g., tin or nickel plating) to enhance solderability and prevent oxidation.
2. Forming and Machining
- Stamping and Cutting: Precision stamping machines cut copper strips into connector terminals with exact dimensions. Accuracy at this stage is crucial to maintain electrical contact reliability.
- Molding: Plastic housing components are formed using injection molding technology. Mold design impacts connector fit, durability, and ease of assembly.
- Surface Finishing: Connectors often receive additional surface treatment such as polishing or coating to improve aesthetics and environmental resistance.
3. Assembly
- Component Insertion: Automated or semi-automated assembly lines insert metal terminals into plastic housings. This step requires precision to ensure secure mechanical locking and optimal electrical contact.
- Soldering and Welding: Some connector designs require soldering wires or contacts. Controlled soldering processes prevent cold joints and maintain conductivity.
- Sealing: For waterproof or outdoor-rated connectors, sealing components like silicone gaskets or heat shrink tubing are integrated to provide IP65 or higher ingress protection.
4. Finishing and Packaging
- Marking: Connectors may be laser-etched or printed with batch numbers, certifications, or polarity indicators.
- Final Inspection: Visual checks and packaging integrity assessments are done to confirm defect-free products.
- Bulk Packaging: Proper packaging protects connectors during transportation and storage, important for international shipments to diverse climates.
Quality Assurance and Control Standards
Quality control (QC) is integral to manufacturing RGB LED strip connectors that meet international buyer expectations. A combination of global quality standards and industry-specific certifications ensures product safety, reliability, and regulatory compliance.
Key International and Industry Standards
- ISO 9001: Most reputable manufacturers implement ISO 9001 quality management systems to ensure consistent production processes, continuous improvement, and customer satisfaction.
- CE Marking: For European buyers, CE certification demonstrates compliance with EU safety, health, and environmental requirements.
- RoHS Compliance: Restriction of hazardous substances ensures connectors are free from lead, mercury, cadmium, and other toxic materials, vital for global markets.
- UL and CSA: These certifications, common in North America but increasingly recognized worldwide, verify electrical safety and performance.
- IP Ratings: Waterproof connectors are tested to meet ingress protection standards (e.g., IP65, IP67), critical for outdoor or industrial applications.
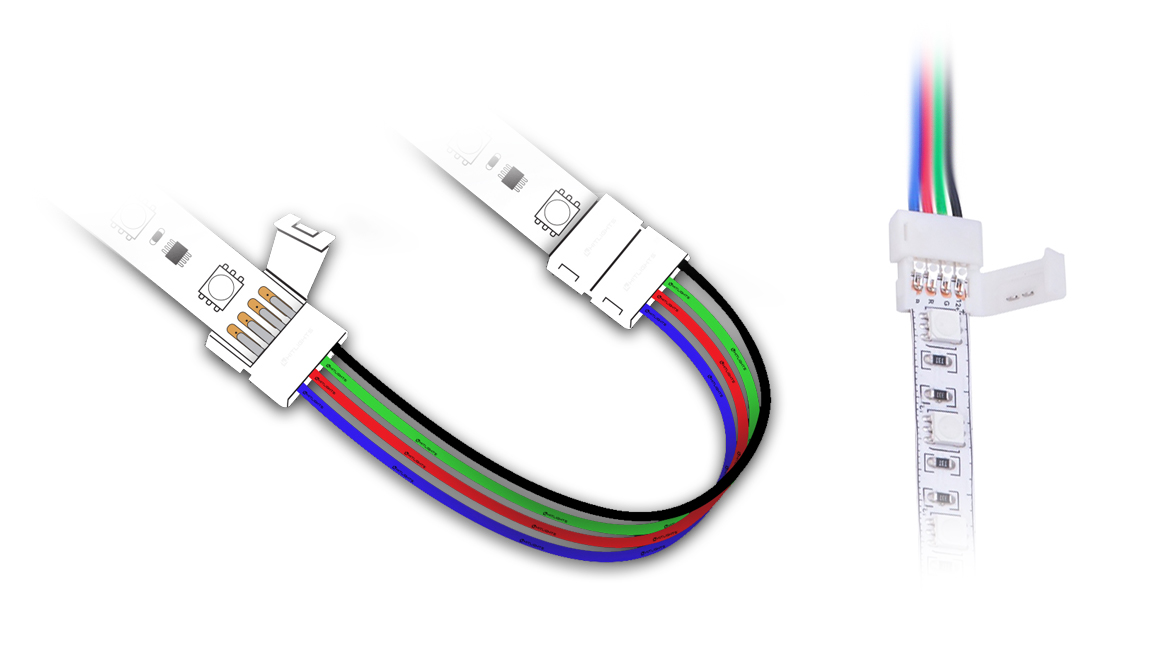
Illustrative Image (Source: Google Search)
Quality Control Checkpoints and Testing Methods
Manufacturers typically implement a layered QC approach throughout production to minimize defects and guarantee performance.
Incoming Quality Control (IQC)
- Material Verification: Raw materials and components are checked for chemical composition, mechanical properties, and dimensional accuracy.
- Supplier Audits: Buyers should request evidence of supplier audits to confirm material quality and traceability.
In-Process Quality Control (IPQC)
- Dimensional Checks: Regular measurements during stamping, molding, and assembly ensure components meet design tolerances.
- Functional Tests: Electrical resistance, continuity, and contact force tests verify connector performance during assembly.
- Visual Inspection: Detects surface defects, assembly errors, or contamination.
Final Quality Control (FQC)
- Electrical Testing: Includes insulation resistance, voltage withstand, and current capacity tests to confirm connectors meet operational specs.
- Environmental Testing: For waterproof connectors, tests such as salt spray, humidity, and thermal cycling simulate real-world conditions.
- Mechanical Durability: Connector insertion and withdrawal force tests, vibration, and drop tests validate mechanical robustness.
How B2B Buyers Can Verify Supplier Quality Control
International buyers should actively engage in supplier quality assurance to mitigate risks associated with product defects or regulatory non-compliance.
1. Factory Audits
- On-site Audits: Physical inspections of manufacturing facilities help assess production capabilities, QC systems, and workforce competence.
- Remote Audits: For buyers unable to visit, virtual audits via video walkthroughs and document reviews are viable alternatives.
2. Documentation and Certification Review
- Quality Certificates: Obtain ISO 9001 certificates, CE declarations, and test reports.
- Test Reports: Request third-party laboratory test results for electrical safety, RoHS compliance, and environmental resistance.
3. Third-Party Inspections
- Pre-shipment Inspections: Independent inspectors verify product quality before shipment, checking sample conformity and packaging.
- Random Sampling: Periodic sampling during production batches can identify quality trends or issues early.
QC and Certification Considerations for International Markets
Buyers from diverse regions face specific challenges and requirements when sourcing RGB LED strip connectors.
Africa and South America
- Regulatory Variations: These regions may have emerging or less harmonized standards. Buyers should prioritize suppliers with international certifications (CE, RoHS) to future-proof investments.
- Climate Challenges: High humidity and temperature fluctuations necessitate connectors with robust environmental sealing and corrosion resistance.
Middle East
- Harsh Environments: Dust, heat, and UV exposure require IP-rated connectors and materials resistant to degradation.
- Customs and Compliance: Buyers should verify that product documentation aligns with local import regulations and electrical safety standards.
Europe (Including Turkey)
- Strict Compliance: European markets demand strict adherence to CE marking, RoHS, and REACH regulations.
- Sustainability Expectations: Increasing focus on eco-friendly materials and manufacturing processes means buyers should assess supplier sustainability credentials.
Southeast Asia (e.g., Indonesia)
- Cost-Performance Balance: Buyers often seek cost-effective connectors without sacrificing quality. Transparent QC data and supplier reliability are key.
- Supply Chain Transparency: Due diligence on supplier traceability and ethical manufacturing practices is increasingly important.
Summary: Strategic Insights for B2B Buyers
- Prioritize suppliers with integrated ISO 9001 quality management systems and relevant international certifications (CE, RoHS, UL).
- Demand detailed QC documentation including IQC, IPQC, and FQC records, supported by third-party test reports.
- Engage in supplier audits or third-party inspections to validate manufacturing capabilities and QC rigor.
- Consider environmental and regulatory factors specific to your market to select connectors with appropriate IP ratings and material certifications.
- Build long-term partnerships with manufacturers who demonstrate transparency, continuous improvement, and responsiveness to quality concerns.
By understanding the manufacturing intricacies and comprehensive quality assurance processes behind RGB LED strip connectors, international B2B buyers can confidently source products that deliver reliable performance, compliance, and value across diverse global markets.
Related Video: Inside LEDYi LED Strip Factory | Full Manufacturing Process by Leading LED Strip Manufacturer
Comprehensive Cost and Pricing Analysis for rgb led strip connector Sourcing
When sourcing RGB LED strip connectors for international B2B projects, understanding the intricate cost structure and pricing dynamics is essential for making informed purchasing decisions. This section breaks down the key cost components, pricing influencers, and strategic buyer tips tailored for stakeholders across Africa, South America, the Middle East, and Europe.
Key Cost Components in RGB LED Strip Connector Production
-
Materials
The primary raw materials include copper contacts, plastic housing (often polycarbonate or ABS), silicone seals for waterproof connectors, and sometimes gold plating for enhanced conductivity. Material costs fluctuate based on global metal prices and polymer availability, directly affecting the base price of connectors. -
Labor
Labor expenses vary significantly by manufacturing location. Countries with established electronics manufacturing hubs tend to have optimized labor costs. However, labor quality impacts assembly precision and product reliability, especially for connectors requiring fine soldering or waterproof sealing. -
Manufacturing Overhead
Overhead includes factory utilities, equipment depreciation, quality assurance infrastructure, and indirect labor. Overhead rates can vary by country and factory scale, influencing overall production costs. -
Tooling and Setup
Injection molding tools for plastic parts and stamping dies for metal contacts represent upfront investments amortized over production volume. Custom connector designs or small batch runs increase tooling costs per unit. -
Quality Control (QC)
Rigorous QC processes, including electrical conductivity tests and waterproofing validation, add to cost but reduce returns and warranty claims. Certifications such as CE, RoHS, or UL compliance also entail testing fees. -
Logistics and Shipping
International shipping costs, import duties, and customs clearance fees vary based on origin, destination, and chosen Incoterms. For regions like Africa and South America, longer transit times and less frequent shipping routes can increase logistics expenses. -
Profit Margin
Suppliers typically factor in a margin to cover business risk and ensure profitability. Margins may vary depending on competitive landscape and buyer-supplier relationship.
Pricing Influencers for RGB LED Strip Connectors
-
Order Volume and Minimum Order Quantity (MOQ)
Larger orders benefit from economies of scale, significantly lowering per-unit prices. MOQ requirements can range from a few hundred to several thousand pieces, impacting initial investment and inventory planning. -
Specifications and Customization
Standard connectors are more cost-effective than custom designs. Customization—such as specific wire lengths, waterproof ratings (IP65/IP67), or unique pin configurations—raises tooling and production complexity. -
Material Quality and Certifications
Connectors made with high-grade copper, gold plating, or certified flame-retardant plastics command premium pricing. Buyers targeting international markets with stringent regulations should prioritize certified products despite higher upfront costs. -
Supplier Location and Capabilities
Suppliers in regions with advanced manufacturing infrastructure often offer better quality control but may have higher labor costs. Conversely, emerging market manufacturers may offer competitive pricing but require thorough supplier vetting. -
Incoterms and Shipping Terms
Pricing varies depending on whether the supplier quotes FOB, CIF, DDP, or EXW terms. Buyers should clarify responsibilities for freight, insurance, and customs to avoid hidden costs.
Strategic Buyer Tips for International B2B Procurement
-
Leverage Volume Negotiations
Consolidate orders or form purchasing groups to negotiate better pricing and reduce MOQ constraints, especially beneficial for buyers in emerging markets with smaller project sizes. -
Evaluate Total Cost of Ownership (TCO)
Consider not only unit price but also potential costs related to installation, maintenance, and warranty service. Higher-quality connectors may reduce long-term operational expenses and downtime. -
Assess Supplier Certifications and Quality Assurance
Prioritize suppliers with internationally recognized certifications to ensure compliance and minimize risks of product failure or customs delays, which is crucial for regulated markets in Europe and the Middle East. -
Understand Pricing Nuances by Region
Buyers in Africa and South America should account for longer lead times and potential import tariffs. In Europe and Turkey, focus on suppliers with local warehouses or distribution centers to reduce delivery times and logistics costs. -
Clarify Incoterms and Shipping Logistics Early
Negotiate clear shipping terms to avoid unexpected freight charges. For instance, requesting DDP (Delivered Duty Paid) can simplify customs clearance but may come at a higher price. -
Request Samples and Conduct Pilot Runs
Prior to large-scale procurement, obtain samples to verify connector compatibility and quality, mitigating risks of costly returns or project delays.
Indicative Pricing Disclaimer
Prices for RGB LED strip connectors vary widely depending on product type, volume, customization, and supplier location. Typical unit costs range from $0.10 to $2.00 USD, with waterproof or specialty connectors at the higher end. Buyers should seek multiple quotes and factor in all ancillary costs to accurately estimate project budgets.
By carefully analyzing these cost factors and adopting strategic procurement approaches, international B2B buyers can optimize sourcing of RGB LED strip connectors to balance cost-efficiency, quality, and supply chain reliability across diverse regional markets.
Spotlight on Potential rgb led strip connector Manufacturers and Suppliers
This section looks at several manufacturers active in the ‘rgb led strip connector’ market. This is a representative sample for illustrative purposes; B2B buyers must conduct extensive due diligence before any transaction. Information is synthesized from public sources and general industry knowledge.
Essential Technical Properties and Trade Terminology for rgb led strip connector
Key Technical Properties of RGB LED Strip Connectors
1. Material Grade
RGB LED strip connectors are typically made from high-quality copper alloys or phosphor bronze for the internal contacts, combined with durable plastic or silicone housing. The choice of material affects electrical conductivity, corrosion resistance, and mechanical durability. For B2B buyers, prioritizing connectors with high-grade materials ensures reliable signal transfer, longer lifespan, and lower maintenance costs, especially critical in humid or industrial environments common in Africa, the Middle East, and South America.
2. Voltage and Current Rating
Connectors must support the voltage (commonly 12V or 24V DC) and current loads of the LED strips they serve. Exceeding these ratings can cause overheating or failure. Understanding these ratings helps buyers specify connectors that match or exceed the power demands of their installations, safeguarding system integrity and reducing warranty claims.
3. Tolerance and Fit Precision
Tolerance refers to the allowable deviation in connector dimensions and contact spacing. Tight manufacturing tolerances ensure secure and stable connections, preventing signal loss or disconnections due to vibration or thermal expansion. B2B buyers benefit from connectors with strict tolerances for commercial-grade applications where system reliability is paramount.
4. Waterproofing and IP Rating
Many RGB LED strip connectors come with IP65, IP67, or higher ingress protection ratings, indicating resistance to dust and water. For outdoor or industrial installations in diverse climates like those in Turkey or Indonesia, waterproof connectors protect the electrical interface from environmental damage, reducing downtime and maintenance.
5. Connection Type Compatibility
Connectors vary by connection style—solderless snap-on, soldered, or screw terminal. Compatibility with specific RGB strip widths (e.g., 10mm) and wiring configurations (4-pin for RGB) is essential. Selecting the correct connection type simplifies installation, reduces labor costs, and improves scalability for large commercial projects.
6. Operating Temperature Range
The connector’s rated temperature range ensures it can perform reliably under expected environmental conditions. For regions with high ambient temperatures or fluctuating climates, choosing connectors rated for wide temperature ranges prevents premature failure and supports continuous operation.
Common Trade and Industry Terms for RGB LED Strip Connectors
OEM (Original Equipment Manufacturer)
Refers to manufacturers who produce connectors that may be branded by other companies. B2B buyers often seek OEM partnerships for customized designs, better pricing, or exclusive supply agreements, enabling differentiation in competitive markets.
MOQ (Minimum Order Quantity)
The smallest quantity a supplier is willing to sell per order. Understanding MOQ helps buyers plan inventory and cash flow, especially when importing to markets like Africa or South America where upfront capital and storage space may be limited.
RFQ (Request for Quotation)
A formal process where buyers solicit pricing and terms from multiple suppliers. RFQs enable buyers to compare costs, lead times, and technical specs, supporting informed procurement decisions and negotiation leverage.
Incoterms (International Commercial Terms)
Standardized trade terms (e.g., FOB, CIF, DDP) defining responsibilities for shipping, insurance, and customs between buyer and seller. Familiarity with Incoterms is crucial for international buyers to manage logistics, costs, and risk effectively.
Lead Time
The time from order placement to delivery. Shorter lead times are vital for projects with tight schedules or seasonal demand, influencing supplier selection and contract terms.
Connector Pin Configuration
Specifies the number and arrangement of electrical contacts (pins). RGB LED strip connectors typically have 4 pins corresponding to Red, Green, Blue, and common positive or negative lines. Correct pin configuration ensures compatibility and proper color control.
Selecting RGB LED strip connectors with a clear understanding of these technical properties and trade terms empowers international B2B buyers to optimize product quality, installation efficiency, and supply chain reliability. This knowledge is especially valuable for buyers operating in diverse global markets with unique environmental and logistical challenges.
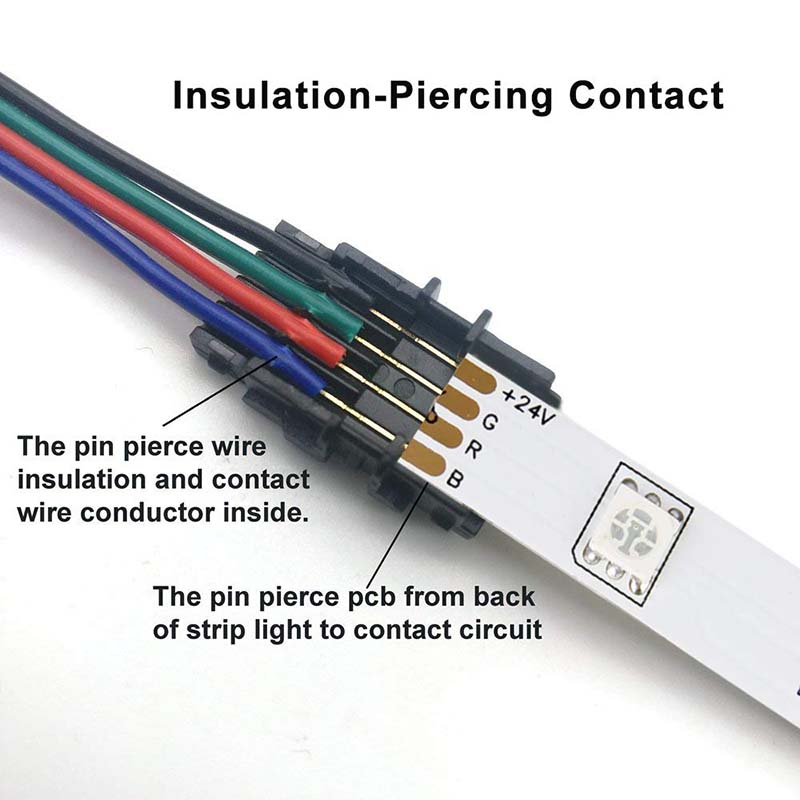
Illustrative Image (Source: Google Search)
Navigating Market Dynamics, Sourcing Trends, and Sustainability in the rgb led strip connector Sector
Market Overview & Key Trends
The global market for RGB LED strip connectors is experiencing robust growth driven by the expanding adoption of LED lighting solutions across commercial, industrial, and residential sectors. Key drivers include increasing urbanization, rising energy efficiency regulations, and growing demand for customizable lighting systems in smart buildings and entertainment venues. For international B2B buyers, particularly in regions such as Africa, South America, the Middle East, and Europe (including emerging markets like Turkey and Indonesia), the focus is shifting towards sourcing connectors that support high reliability, ease of installation, and compatibility with diverse LED strip formats.
Technological advancements are shaping sourcing trends in this sector. Waterproof and IP-rated connectors are becoming standard, catering to outdoor and industrial applications in harsh environments common in many emerging markets. Additionally, quick-connect and solderless designs are gaining traction as they reduce installation time and labor costs, critical factors for large-scale projects. Buyers are increasingly prioritizing connectors compatible with 12V and 24V systems, reflecting the prevalent use of these voltage standards globally.
Market dynamics are also influenced by supply chain considerations. Buyers from Africa and South America face challenges such as longer lead times and import duties, encouraging them to seek regional manufacturing partnerships or suppliers with robust logistics networks. Meanwhile, European and Middle Eastern buyers emphasize certifications and compliance with international standards (e.g., CE, RoHS) to meet local regulations and quality expectations. The rise of e-commerce platforms and digital sourcing tools further empowers buyers to compare products, verify supplier credentials, and negotiate better terms.
Actionable Insight: International buyers should evaluate suppliers not only on product specifications but also on their ability to provide technical support, customization options, and reliable after-sales service. Building strategic relationships with manufacturers who understand local market nuances and regulatory requirements can mitigate risks and optimize procurement costs.
Sustainability & Ethical Sourcing in B2B
Sustainability has become a critical factor in the procurement of RGB LED strip connectors, reflecting broader global trends towards environmentally responsible manufacturing and supply chains. The environmental impact of connector production involves raw material extraction—primarily plastics and metals such as copper—and energy-intensive processes that contribute to carbon emissions. Consequently, B2B buyers are increasingly demanding products that minimize ecological footprints through the use of recycled materials, low-impact manufacturing techniques, and design for recyclability.
Ethical sourcing is equally important, especially for buyers operating in regions with growing scrutiny on labor practices and corporate social responsibility. Ensuring that suppliers adhere to fair labor standards, avoid conflict minerals, and maintain transparency throughout the supply chain is essential to uphold brand reputation and comply with international regulations such as the EU Conflict Minerals Regulation.
Many manufacturers now offer connectors certified under environmental standards like RoHS (Restriction of Hazardous Substances) and REACH (Registration, Evaluation, Authorization and Restriction of Chemicals), which guarantee reduced hazardous content and safer chemical use. Additionally, certifications such as ISO 14001 for environmental management systems provide assurance of ongoing sustainability efforts.
Actionable Insight: Buyers should incorporate sustainability criteria into their supplier evaluation frameworks, requesting documentation on material sourcing, energy usage, and waste management. Prioritizing suppliers who invest in ‘green’ innovations—such as biodegradable plastics or lead-free solder—can help companies meet their ESG goals while mitigating regulatory risks and appealing to environmentally conscious end customers.
Evolution and Historical Context
The RGB LED strip connector sector has evolved significantly alongside advances in LED lighting technology. Initially, connectors were simple, often requiring manual soldering, which limited scalability and increased installation errors. As LED strips became popular for decorative and architectural lighting in the early 2000s, demand surged for connectors that simplified installation and enhanced durability.
The introduction of snap-on and quick-connect connectors revolutionized the market by enabling tool-free assembly, reducing labor costs, and expanding the applications of LED strips into more complex layouts. Subsequently, waterproof and weather-resistant connectors emerged, responding to the need for outdoor and industrial-grade lighting solutions.
Today, the sector emphasizes modularity, compatibility with diverse LED strip types, and integration with smart lighting controls. This evolution underscores the importance for B2B buyers to stay informed on product innovations that can optimize system design, installation efficiency, and lifecycle management in their projects.
Related Video: Incoterms for beginners | Global Trade Explained
Frequently Asked Questions (FAQs) for B2B Buyers of rgb led strip connector
-
How can I effectively vet suppliers of RGB LED strip connectors for international B2B purchases?
To vet suppliers, start by verifying their business licenses and certifications relevant to electrical components, such as CE, RoHS, or UL marks. Request detailed product datasheets and inquire about production capabilities and quality control processes. Check references and reviews from other international buyers, especially from regions like Africa and the Middle East, to gauge reliability. Additionally, consider suppliers who offer transparent communication, factory audits (either virtual or physical), and sample shipments to assess connector quality before placing large orders. -
Are customization options available for RGB LED strip connectors, and how should I approach this with suppliers?
Yes, many manufacturers provide customization services including connector size, wire length, waterproofing level, and color coding to match specific LED strip models. When discussing customization, clearly specify your technical requirements, intended use environment, and compliance standards needed for your target markets. Expect minimum order quantities (MOQs) for customized products and longer lead times. Negotiate upfront on design approval processes and prototype samples to avoid miscommunication and ensure the final product meets your exact needs. -
What are typical MOQ and lead times for RGB LED strip connectors in international B2B trade?
MOQ varies by supplier and customization level, typically ranging from 500 to 5,000 pieces per SKU. Standard connector models usually have lower MOQs and shorter lead times of 2–4 weeks, while customized connectors may require 6–8 weeks or more. Plan your procurement schedule accordingly and confirm production capacity during supplier negotiations. For buyers in regions with longer shipping times, such as South America or Africa, factor in logistics lead time to ensure timely inventory replenishment. -
Which payment terms are common and advisable when sourcing RGB LED strip connectors from overseas suppliers?
Common payment terms include a 30% deposit upfront with the balance paid before shipment or via a Letter of Credit (L/C) for larger orders. For trusted suppliers, net 30 or net 60 days terms might be negotiated. To minimize risk, use secure payment methods such as PayPal, escrow services, or trade assurance platforms. Always confirm payment terms in the contract, clearly outlining penalties for late payment or shipment delays, and consider using third-party inspection services to verify product quality before final payment. -
What quality assurance measures should I expect from suppliers of RGB LED strip connectors?
Suppliers should provide evidence of consistent quality through certifications like ISO 9001 and compliance with international safety standards (e.g., CE, RoHS). They should conduct in-line inspections during production and final testing of connectors for electrical continuity, waterproof rating, and mechanical durability. Ask for quality control reports and sample test certificates. For large orders, arrange third-party quality inspections or factory audits to verify compliance before shipment, reducing the risk of defective products impacting your supply chain. -
How do I manage logistics and shipping challenges when importing RGB LED strip connectors internationally?
Choose suppliers experienced in international shipping with knowledge of customs procedures in your country. Confirm Incoterms (e.g., FOB, CIF) to clarify responsibilities for freight and insurance. For regions with complex import regulations like the Middle East or Turkey, ensure correct HS codes and documentation to avoid customs delays. Opt for consolidated shipments when possible to reduce freight costs and request tracking updates. Collaborate with reliable freight forwarders familiar with your local ports to streamline clearance and last-mile delivery. -
What steps can I take to resolve disputes or quality issues with RGB LED strip connector suppliers?
Establish clear contract terms including product specifications, inspection protocols, and dispute resolution procedures before ordering. If issues arise, document discrepancies with photos and test results, then communicate promptly and professionally with the supplier. Use mediation or arbitration clauses if included in the contract to avoid costly litigation. Maintain open dialogue to negotiate partial refunds, replacements, or discounts. For recurrent problems, consider switching suppliers or engaging third-party quality assurance firms for future orders. -
Are there regional considerations when sourcing RGB LED strip connectors for markets in Africa, South America, or the Middle East?
Yes, regional factors such as climate, voltage standards, and local certifications impact product suitability. For example, waterproof connectors are essential in humid or outdoor African environments, while Middle Eastern markets may require connectors compliant with specific electrical safety standards. Additionally, supplier proximity and shipping routes affect lead times and costs. Engage suppliers who understand these regional nuances and can tailor products accordingly. Also, consider local regulations and import tariffs to ensure competitive pricing and timely delivery.
Important Disclaimer & Terms of Use
⚠️ Important Disclaimer
The information provided in this guide, including content regarding manufacturers, technical specifications, and market analysis, is for informational and educational purposes only. It does not constitute professional procurement advice, financial advice, or legal advice.
While we have made every effort to ensure the accuracy and timeliness of the information, we are not responsible for any errors, omissions, or outdated information. Market conditions, company details, and technical standards are subject to change.
B2B buyers must conduct their own independent and thorough due diligence before making any purchasing decisions. This includes contacting suppliers directly, verifying certifications, requesting samples, and seeking professional consultation. The risk of relying on any information in this guide is borne solely by the reader.
Strategic Sourcing Conclusion and Outlook for rgb led strip connector
Effective sourcing of RGB LED strip connectors is pivotal for delivering reliable, high-performance lighting solutions in diverse commercial and industrial settings. For international B2B buyers across Africa, South America, the Middle East, and Europe, understanding the nuances of connector types, wiring configurations, and quality standards ensures compatibility and longevity of installations. Prioritizing robust connection methods, appropriate wire gauge selection, and waterproofing options tailored to local environmental conditions significantly reduces maintenance costs and operational downtime.
Strategic sourcing also means partnering with suppliers who offer comprehensive technical support, certified products, and scalable solutions that align with evolving project demands. Leveraging insights on power distribution and connector compatibility can enhance system efficiency and future-proof your lighting infrastructure.
Looking ahead, the increasing adoption of smart and energy-efficient lighting technologies will drive demand for advanced RGB connectors with enhanced durability and integration capabilities. Buyers in emerging and established markets should proactively engage with manufacturers to explore customizable, cost-effective solutions that meet international standards and local regulatory requirements.
Take action now: invest in thorough supplier evaluation and technical due diligence to secure RGB LED strip connectors that not only meet today’s specifications but also empower your projects to adapt seamlessly to tomorrow’s innovations.