Introduction: Navigating the Global Market for joining led strips
Joining LED strips is a pivotal step in designing versatile and scalable lighting solutions that meet diverse industrial and commercial needs. For international B2B buyers, especially those operating across Africa, South America, the Middle East, and Europe—including emerging markets like Indonesia and Poland—understanding the nuances of joining LED strips is essential to optimize product performance, installation efficiency, and cost-effectiveness.
This guide delves into the critical aspects of joining LED strips, covering a comprehensive range of topics such as the different types of LED strips and connectors, key materials and technologies used in manufacturing, quality control standards, and the spectrum of reliable global suppliers. It also offers detailed insights into pricing structures and market trends that influence procurement decisions in various regions.
By navigating through this guide, buyers will gain actionable knowledge on selecting the right joining methods—whether soldering, clip connectors, or specialized adhesive solutions—to ensure durability and seamless integration. Additionally, the guide addresses common challenges and frequently asked questions that arise during installation and customization, empowering buyers to troubleshoot and avoid costly errors.
Armed with this authoritative resource, international B2B buyers can confidently evaluate suppliers, negotiate favorable terms, and implement LED strip joining solutions that align with their project specifications and budget constraints. This strategic understanding is vital for maximizing ROI and maintaining competitive advantage in the dynamic global LED lighting market.
Understanding joining led strips Types and Variations
Type Name | Key Distinguishing Features | Primary B2B Applications | Brief Pros & Cons for Buyers |
---|---|---|---|
Soldered Connections | Permanent electrical join via soldering on copper pads | Custom installations, high-reliability projects | + Strong, durable connection – Requires skilled labor and tools |
Clip-on Connectors | Tool-free connectors that clamp LED strip ends together | Quick installations, prototyping, temporary setups | + Easy and fast to use – Less durable, potential contact issues |
Flexible PCB Connectors | Specialized connectors for flexible LED strip PCBs | Curved or irregular surface installations | + Maintains flexibility and integrity – Higher cost, limited availability |
Adhesive-backed Joiners | Joiners with adhesive pads for mechanical and electrical joining | Retail display setups, modular lighting systems | + Simple installation, no tools needed – Lower electrical reliability |
Wireless Connectors | Connect LED strips via wireless control modules (no physical join) | Smart lighting systems, IoT-enabled projects | + Enables remote control and modularity – Higher upfront cost, complexity |
Soldered Connections
Soldered joins are the most traditional and reliable method for connecting LED strips, involving melting solder on copper pads to ensure strong electrical and mechanical bonds. This type is ideal for projects requiring long-term durability and minimal maintenance, such as architectural lighting or industrial applications. B2B buyers should consider the availability of skilled technicians and the cost of labor, as well as the need for precise cutting and alignment to avoid damage.
Clip-on Connectors
Clip-on connectors provide a fast, tool-free solution for joining LED strips by physically clamping the strip ends. These are highly suitable for rapid prototyping, temporary installations, or projects with frequent reconfiguration needs such as trade shows or retail environments. Buyers benefit from reduced labor costs but should be aware of potential downsides like less reliable electrical contact and susceptibility to disconnection in high-vibration environments.
Flexible PCB Connectors
Designed specifically for flexible LED strip PCBs, these connectors maintain the strip’s bendability and are essential in installations on curved or irregular surfaces, common in automotive, signage, and specialty architectural lighting. They offer a balance between flexibility and electrical integrity but come at a premium price and may require sourcing from specialized suppliers, which is a key consideration for international buyers.
Adhesive-backed Joiners
These joiners use adhesive pads to mechanically and electrically connect LED strips without the need for tools or soldering. Ideal for modular lighting systems and retail displays where ease of installation and reusability are priorities, they simplify logistics and reduce installation time. However, buyers should evaluate the electrical reliability and environmental resistance of adhesives, especially for outdoor or industrial use.
Wireless Connectors
Wireless LED strip joining eliminates physical wiring by connecting strips via wireless control modules, supporting IoT integration and smart lighting projects. This variation is well-suited for modern, connected environments requiring flexible control, such as smart buildings or large-scale installations. While offering advanced functionality and modularity, buyers must factor in higher initial costs, potential interference issues, and the need for compatible control systems.
Related Video: How to Connect LED Strips Using Various Connectors
Key Industrial Applications of joining led strips
Industry/Sector | Specific Application of joining led strips | Value/Benefit for the Business | Key Sourcing Considerations for this Application |
---|---|---|---|
Retail & Commercial | Seamless lighting for display cases and signage | Enhances product visibility and customer experience | Consistent color temperature, durability, ease of installation |
Architecture & Interior Design | Continuous ambient and accent lighting in large spaces | Creates uniform lighting effects, aesthetic appeal | Flexibility of strip length, IP rating for moisture resistance |
Automotive & Transportation | Integrated lighting in vehicle interiors and signage | Improves safety and brand visibility | Vibration resistance, heat dissipation, compatibility with vehicle power |
Hospitality & Leisure | Mood and decorative lighting in hotels, restaurants, and entertainment venues | Enhances ambiance and guest satisfaction | Customizable length, dimmability, compliance with local electrical standards |
Industrial & Manufacturing | Task lighting and machine indicator lighting | Improves operational efficiency and safety | Robust connectors, ease of maintenance, resistance to dust and chemicals |
Joining LED strips is essential for creating continuous, uninterrupted lighting runs in various industrial contexts. In retail and commercial environments, joined LED strips enable seamless illumination of display cases and signage, enhancing product visibility and attracting customers. Buyers from emerging markets such as Africa and South America should prioritize sourcing LED strips with consistent color temperature and reliable connectors to ensure uniform lighting and minimize maintenance costs.
In architecture and interior design, joining LED strips allows for flexible, extended ambient or accent lighting solutions in large residential or commercial spaces. European and Middle Eastern buyers often require LED strips with high IP ratings for moisture resistance, especially in bathrooms or outdoor areas, ensuring longevity and compliance with local building codes.
The automotive and transportation sector utilizes joined LED strips for interior cabin lighting and external signage, where continuous lighting improves safety and brand presence. Buyers in regions with harsh climates, such as parts of the Middle East, should focus on LED strips with enhanced heat dissipation and vibration-resistant connectors to withstand operational stresses.
For hospitality and leisure industries, joined LED strips provide customizable mood lighting that elevates guest experience in hotels and entertainment venues. International buyers, including those from Indonesia and Poland, benefit from sourcing dimmable LED strips compatible with local electrical standards, allowing tailored ambiance control and energy savings.
Lastly, in industrial and manufacturing settings, joined LED strips serve as task lighting and machine status indicators, improving safety and workflow efficiency. Buyers must consider robust, dust- and chemical-resistant connectors to ensure durability in demanding environments, which is critical for facilities in Africa and South America where industrial conditions may be challenging.
Selecting the right LED strip joining solutions tailored to each industry’s unique requirements can significantly enhance operational performance and customer satisfaction for B2B buyers worldwide.
Strategic Material Selection Guide for joining led strips
Silicone-Based Adhesives and Sealants
Silicone adhesives are widely used for joining LED strips due to their excellent flexibility, high temperature resistance (typically up to 200°C), and outstanding weatherproofing properties. These materials provide robust protection against moisture and UV exposure, making them ideal for outdoor or humid environments. Their chemical inertness ensures corrosion resistance, which is critical for long-term durability in diverse climates.
Pros: Silicone adhesives offer excellent elasticity, which accommodates thermal expansion and contraction of LED strips without cracking. They also provide strong adhesion on various substrates like aluminum and plastics, commonly used in LED strip installations. Cons: The curing process can be slower compared to other adhesives, and silicone materials tend to have a higher cost, which might impact budget-sensitive projects. Additionally, their surface can be challenging to paint or coat after application.
Application Impact: Silicone adhesives are particularly suited for applications requiring waterproofing, such as outdoor signage or architectural lighting in tropical or coastal regions like parts of Africa and South America.
International Considerations: Buyers in regions such as the Middle East and Europe should verify compliance with standards like ASTM C920 (Standard Specification for Elastomeric Joint Sealants) or DIN EN ISO 11600 to ensure product reliability. In markets like Indonesia and Poland, preference for silicone adhesives is growing due to their versatility and longevity in varied climatic conditions.
Epoxy Resins
Epoxy resins are a common choice for permanent, high-strength bonding of LED strips, especially in industrial and commercial settings. They exhibit excellent mechanical strength, chemical resistance, and temperature tolerance (up to 150°C). Epoxies cure to form rigid bonds that provide electrical insulation and environmental protection.
Pros: Epoxy adhesives deliver superior durability and resistance to solvents and abrasion, making them suitable for harsh environments. They also allow for precise application and quick curing with appropriate formulations. Cons: Their rigidity can be a drawback where flexibility is required, potentially leading to stress fractures in dynamic or flexible LED strip installations. Epoxies are generally more complex to handle, requiring mixing and precise application conditions.
Application Impact: Ideal for fixed installations where LED strips are mounted on rigid surfaces and where mechanical strength is paramount, such as industrial lighting in factories or retail environments in Europe and the Middle East.
International Considerations: Compliance with standards like ISO 9001 for manufacturing quality and regional chemical safety regulations (e.g., REACH in Europe) is essential. Buyers in South America and Africa should consider local availability of certified epoxy products and the need for technical support during installation.
Polyurethane Adhesives
Polyurethane (PU) adhesives offer a balanced combination of flexibility and strength, with good resistance to abrasion, chemicals, and temperature variations (typically up to 120°C). PU adhesives are known for their strong bonding on a variety of materials including metals, plastics, and glass.
Pros: These adhesives provide moderate flexibility, which helps absorb vibrations and impacts, reducing the risk of LED strip damage. They cure relatively quickly and offer good resistance to moisture and UV degradation. Cons: PU adhesives can be sensitive to humidity during application, requiring controlled environments for optimal curing. Their chemical composition may also cause yellowing over time under intense UV exposure.
Application Impact: Suitable for indoor and semi-outdoor LED installations, such as retail displays or decorative lighting in commercial spaces across Europe and the Middle East, as well as in emerging markets in Africa and South America where moderate environmental resistance is sufficient.
International Considerations: Buyers should verify compliance with ASTM D3498 (Standard Specification for Polyurethane Adhesives) and consider local climate conditions that may affect curing and longevity. In countries like Indonesia and Poland, PU adhesives are favored for their cost-effectiveness and ease of use.
Heat-Shrink Tubing with Adhesive Lining
Heat-shrink tubing with an inner adhesive lining is a specialized material used for joining and protecting LED strip connections, providing both mechanical support and environmental sealing. These materials typically withstand temperatures up to 125°C and offer excellent resistance to moisture and abrasion.
Pros: This method provides a clean, insulated, and durable joint that protects against dust, water ingress, and mechanical strain. It is relatively easy to apply with heat guns, making it suitable for field installations. Cons: Heat-shrink tubing requires precise sizing and access to heat application tools, which may increase installation complexity. It is less suitable for continuous flexible sections due to rigidity after shrinking.
Application Impact: Ideal for electrical connections and splices in LED strip installations exposed to outdoor or industrial conditions, such as outdoor signage in the Middle East or humid environments in South America.
International Considerations: Buyers should ensure products meet IEC 60684-3 (Standard on Heat-Shrinkable Tubing) and regional electrical safety standards. In Africa and Indonesia, availability of heat-shrink tubing with certified adhesive linings is growing, supporting safer and more reliable LED strip connections.
Material | Typical Use Case for joining led strips | Key Advantage | Key Disadvantage/Limitation | Relative Cost (Low/Med/High) |
---|---|---|---|---|
Silicone-Based Adhesives | Outdoor and humid environment LED strip sealing | Excellent flexibility and weather resistance | Higher cost and slower curing | High |
Epoxy Resins | Industrial and rigid surface LED strip bonding | Superior mechanical strength and chemical resistance | Rigid bond unsuitable for flexible applications | Medium |
Polyurethane Adhesives | Indoor and semi-outdoor decorative or retail lighting | Balanced flexibility and strong adhesion | Sensitive to humidity during curing | Medium |
Heat-Shrink Tubing with Adhesive Lining | Electrical connection protection in outdoor/industrial settings | Provides insulated, sealed, and durable joints | Requires heat application tools and precise sizing | Medium |
In-depth Look: Manufacturing Processes and Quality Assurance for joining led strips
Overview of Manufacturing Processes for Joining LED Strips
The manufacturing of joining components for LED strips involves several critical stages designed to ensure product reliability, electrical integrity, and ease of installation. Understanding these stages enables B2B buyers to evaluate potential suppliers based on their production capabilities and quality control rigor.
1. Material Preparation
High-quality raw materials form the foundation of reliable LED strip connectors and joining modules. Typically, manufacturers source:
- Copper or copper alloy conductors for optimal electrical conductivity.
- Flexible printed circuit boards (FPCBs) or rigid substrates, depending on the application.
- Insulating materials such as silicone or PVC for waterproofing and mechanical protection.
- Adhesives and sealants for bonding and environmental resistance.
Material inspection at this stage ensures that only compliant inputs proceed, mitigating risks of failure due to substandard components.
2. Forming and Fabrication
This stage includes precision cutting, stamping, and shaping of metal contacts and substrates to exact dimensions. Techniques commonly used:
- Stamping and punching for creating contact points and connection pads.
- Lamination to combine flexible substrates with conductive traces.
- Injection molding for plastic housings, ensuring durability and protection.
Advanced CNC machines and automated fabrication lines help maintain tight tolerances, essential for consistent electrical connections and mechanical fit.
3. Assembly
Assembly integrates the conductive elements with insulating materials and mechanical housings. Key processes include:
- Soldering or ultrasonic welding to attach electrical contacts securely to the LED strip pads.
- Connector insertion and locking mechanisms to ensure stable mechanical joins.
- Application of waterproofing elements like silicone coatings or heat shrink tubing for outdoor or damp environments.
Many manufacturers employ automated pick-and-place machines coupled with robotic soldering to increase precision and repeatability.
4. Finishing and Packaging
Final steps focus on product protection and logistics readiness:
- Cleaning to remove flux residues and contaminants.
- Marking with batch numbers and compliance labels.
- Protective packaging designed to prevent damage during transportation, often customized for bulk B2B orders.
Efficient finishing processes minimize defects and support traceability throughout the supply chain.
Quality Assurance Framework in Joining LED Strip Manufacturing
Robust quality assurance (QA) is essential to guarantee that joining components meet international standards and perform reliably under diverse environmental conditions. For B2B buyers, understanding QA frameworks helps in supplier evaluation and risk mitigation.
Relevant International Standards
- ISO 9001: The globally recognized standard for quality management systems. Suppliers with ISO 9001 certification demonstrate consistent process control and continual improvement.
- CE Marking (Europe): Indicates compliance with European safety, health, and environmental requirements, crucial for buyers targeting EU markets.
- RoHS Compliance: Restricts hazardous substances in electronic components, aligning with environmental regulations in many regions.
- UL Certification (North America): Relevant if products are intended for markets requiring safety certification.
- IP Ratings: Define ingress protection levels, especially important for outdoor or industrial LED strip applications.
Buyers should verify that suppliers maintain certifications relevant to their target markets.
Key Quality Control Checkpoints
- Incoming Quality Control (IQC): Inspection of raw materials and components upon receipt. Includes dimensional checks, material composition tests, and visual inspections.
- In-Process Quality Control (IPQC): Continuous monitoring during assembly. Common checks include solder joint integrity, connector fit tests, and electrical continuity measurements.
- Final Quality Control (FQC): Comprehensive testing of finished products before shipment. Includes functional tests, visual defect inspection, and packaging verification.
This layered QC approach ensures defects are identified and corrected early, reducing waste and improving reliability.
Common Testing Methods
- Electrical Testing: Resistance, continuity, and insulation resistance tests confirm proper electrical performance.
- Mechanical Testing: Tensile and flex tests on connectors simulate real-world handling stresses.
- Environmental Testing: Exposure to humidity, temperature cycling, and UV light to assess durability, particularly for outdoor applications.
- Visual Inspection: Automated optical inspection (AOI) or manual checks identify physical defects or assembly errors.
Buyers can request detailed test reports to confirm adherence to specifications.
Verifying Supplier Quality Assurance: Practical Guidance for B2B Buyers
For international buyers from Africa, South America, the Middle East, and Europe, verifying supplier QC practices is crucial to ensure product consistency and compliance.
Conducting Supplier Audits
- On-site audits: Visiting manufacturing facilities to observe production processes, QC labs, and storage conditions firsthand.
- Remote audits: Leveraging video calls and digital documentation review when travel is restricted.
- Key audit focus areas include process controls, equipment calibration, staff training, and record-keeping.
Reviewing Quality Documentation
- Request Certificates of Conformity for relevant standards (ISO 9001, CE, RoHS).
- Obtain Test Reports from internal QC or accredited third-party labs.
- Examine Material Traceability Records to ensure batch-level accountability.
Utilizing Third-Party Inspection Services
- Independent inspections by recognized agencies (e.g., SGS, Intertek) provide unbiased product verification.
- Inspections can cover pre-shipment checks, random sampling, and compliance audits.
- Third-party reports add credibility and confidence, especially for buyers unfamiliar with the supplier.
QC and Certification Nuances for Diverse International Markets
Different regions have specific regulatory environments and buyer expectations that impact QC and certification requirements.
- Africa & Middle East: Buyers often prioritize durability and environmental resistance due to harsh climates. Certifications like IP ratings and RoHS are increasingly important. Some countries require local testing or certification for import clearance.
- South America: Compliance with local electrical safety standards (e.g., INMETRO in Brazil) may be mandatory. Buyers benefit from suppliers who can provide bilingual documentation and regional compliance support.
- Europe (including Poland): High emphasis on CE marking, RoHS, and REACH regulations. Strict environmental and safety standards mean buyers should prioritize suppliers with proven compliance and transparent quality systems.
- Southeast Asia (e.g., Indonesia): Buyers may look for cost-effective solutions but still require adherence to international safety and quality norms. Familiarity with local import regulations and certifications can streamline procurement.
Actionable Insights for B2B Buyers
- Prioritize suppliers with certified quality management systems (ISO 9001) and relevant product certifications (CE, RoHS).
- Request detailed quality control plans and testing protocols to ensure alignment with your project requirements.
- Insist on material traceability and batch-level documentation to enhance supply chain transparency.
- Leverage third-party inspection services to independently verify supplier claims, especially when sourcing from new or distant manufacturers.
- Understand regional certification requirements early to avoid import delays and ensure market acceptance.
- Incorporate quality assurance milestones into your procurement contracts to enforce accountability.
By rigorously evaluating manufacturing processes and quality assurance systems, international B2B buyers can secure reliable joining components for LED strips that meet performance expectations and regulatory demands across diverse markets.
Related Video: LED Light Making Process | How LED Lights Made Inside Factory | Manufacturing Process
Comprehensive Cost and Pricing Analysis for joining led strips Sourcing
Key Cost Components in Joining LED Strips
Understanding the cost structure behind joining LED strips is essential for international B2B buyers aiming to optimize procurement and project budgets. The primary cost components include:
- Materials: This covers the cost of LED strip connectors, solder, wiring, heat shrink tubing, and any additional components such as mounting brackets or protective casings. Material quality directly influences durability and performance.
- Labor: Skilled labor is required for cutting, soldering, connecting, and testing LED strips. Labor costs vary widely depending on the manufacturing location and expertise level.
- Manufacturing Overhead: This includes utilities, factory maintenance, equipment depreciation, and indirect labor costs that support production.
- Tooling: Specialized tools for cutting, soldering, and connector crimping represent upfront and ongoing expenses. For custom joining solutions, tooling costs may increase.
- Quality Control (QC): Rigorous testing to ensure electrical safety, continuity, and consistent light output adds to costs but reduces risk of returns or failures.
- Logistics: Shipping, customs duties, and handling fees can be significant for international buyers. Packaging for fragile LED components also impacts logistics expenses.
- Margin: Suppliers include profit margins to cover business risks and growth, typically influenced by market competition and order size.
Price Influencers Affecting LED Strip Joining Solutions
Pricing in LED strip joining is dynamic and shaped by several factors:
- Order Volume and Minimum Order Quantities (MOQ): Larger orders often benefit from economies of scale, driving down unit costs. Buyers from emerging markets should inquire about MOQ flexibility to avoid overstocking.
- Specifications and Customization: Custom lengths, specialized connectors (e.g., waterproof or flexible types), and integration with smart lighting controllers increase costs.
- Material Selection: Premium materials such as gold-plated connectors or high-grade solder raise prices but enhance longevity and electrical performance.
- Quality Certifications: Compliance with international standards (e.g., CE, RoHS, UL) adds assurance but may increase costs due to testing and certification fees.
- Supplier Factors: Supplier reputation, production capacity, and geographic location influence pricing. Established manufacturers with streamlined processes may offer better value.
- Incoterms and Delivery Terms: Terms like FOB, CIF, or DDP significantly affect total landed cost. Buyers must factor in who bears shipping risk and customs clearance responsibilities.
Actionable Buyer Tips for International B2B Procurement
For buyers from Africa, South America, the Middle East, and Europe, including markets such as Indonesia and Poland, consider the following strategies to achieve cost-effective sourcing:
- Negotiate Volume Discounts and Flexible MOQs: Engage suppliers early to discuss tiered pricing structures and MOQ adjustments that suit your project scale.
- Prioritize Total Cost of Ownership (TCO): Look beyond unit price by factoring in installation ease, reliability, warranty terms, and after-sales support. Lower upfront costs may lead to higher maintenance expenses.
- Evaluate Quality vs. Price Trade-offs: While lower-cost connectors and materials reduce initial expenditure, they can compromise product lifespan and cause frequent replacements.
- Clarify Incoterms to Avoid Hidden Fees: Confirm delivery terms to anticipate customs duties, taxes, and freight costs accurately. For regions with complex import regulations, DDP (Delivered Duty Paid) can simplify transactions.
- Leverage Local Expertise: Partner with local agents or distributors who understand regional import procedures and can facilitate smoother logistics.
- Request Samples and Conduct Testing: Before committing to large orders, obtain product samples to verify build quality and compatibility with your LED strips.
- Consider Supplier Certifications and Compliance: Certifications aligned with your local regulatory requirements ensure smoother market entry and reduce liability risks.
Indicative Pricing Disclaimer
Pricing for joining LED strips varies widely depending on product specifications, order size, and supplier location. The figures mentioned in market references should be regarded as indicative and subject to negotiation. Buyers are encouraged to request detailed quotations and conduct comparative analyses to tailor procurement decisions to their unique operational contexts.
By dissecting the cost drivers and pricing influencers, international B2B buyers can make informed decisions when sourcing LED strip joining solutions, balancing quality, price, and operational efficiency for optimal project outcomes.
Spotlight on Potential joining led strips Manufacturers and Suppliers
This section looks at several manufacturers active in the ‘joining led strips’ market. This is a representative sample for illustrative purposes; B2B buyers must conduct extensive due diligence before any transaction. Information is synthesized from public sources and general industry knowledge.
Essential Technical Properties and Trade Terminology for joining led strips
Critical Technical Properties for Joining LED Strips
When sourcing LED strip joining components, understanding these key technical specifications ensures compatibility, durability, and optimal performance for your projects.
-
Material Grade and Conductivity
Connectors and solder pads are commonly made from copper or copper alloys with surface finishes like tin or gold plating. High-grade materials guarantee excellent electrical conductivity and corrosion resistance, critical for maintaining consistent lighting and preventing signal loss, especially in humid or outdoor environments common in Africa, South America, and the Middle East. -
Voltage and Current Ratings
LED strips and their connectors must match in voltage (commonly 12V or 24V) and current capacity. Exceeding these ratings can cause overheating or failure. B2B buyers should verify these ratings to ensure safety and longevity, particularly for large-scale installations in commercial or industrial settings. -
Tolerance and Precision in Cutting and Joining
LED strips have designated cutting points with precise spacing (often every 5cm or 10cm). Accurate cutting tolerance ensures that connectors fit perfectly, avoiding damage to LED circuits. This precision impacts installation efficiency and reduces waste, vital for cost-sensitive markets like Poland or Indonesia. -
Waterproofing and IP Rating
For outdoor or moisture-prone applications, connectors and joined strips should meet appropriate IP ratings (e.g., IP65 or higher). Waterproof joining methods, such as silicone sealants or specialized connectors, prevent short circuits and extend product lifespan in harsh climates, a key consideration for buyers in tropical or desert regions. -
Flexibility and Bending Radius
LED strips and their connectors must support the required bending radius without cracking or losing electrical contact. Flexible joints are essential for architectural lighting or custom installations. Understanding this helps buyers choose solutions that reduce installation time and rework. -
Compatibility with Control Systems
Some LED strips incorporate smart features requiring connectors compatible with RGB, RGBW, or addressable LED controllers. Ensuring connectors support the necessary signal types is crucial for seamless integration in smart lighting projects across Europe and emerging smart city markets globally.
Common Industry and Trade Terms for LED Strip Joining
Familiarity with these terms empowers buyers to communicate effectively with suppliers and streamline procurement.
-
OEM (Original Equipment Manufacturer)
Refers to companies that produce components or products sold under another brand. Buyers interested in private labeling or custom designs often work directly with OEMs to reduce costs and tailor products to specific market needs. -
MOQ (Minimum Order Quantity)
The smallest quantity a supplier is willing to sell. Understanding MOQ helps buyers plan inventory and negotiate better pricing, especially important for businesses operating in markets like South America or Africa where demand volumes can vary significantly. -
RFQ (Request for Quotation)
A formal inquiry sent to suppliers asking for price, lead time, and terms for specific products. RFQs are essential in B2B transactions to compare offers and ensure transparency in purchasing LED joining components. -
Incoterms (International Commercial Terms)
Standardized trade terms defining responsibilities between buyers and sellers regarding shipping, insurance, and tariffs. Common terms include FOB (Free On Board) and CIF (Cost, Insurance, and Freight). Understanding Incoterms helps buyers manage logistics and cost allocation, crucial for international trade across diverse regions. -
Solderless Connector
A type of LED strip connector that does not require soldering, allowing quick and tool-free joining. These connectors reduce installation time and are preferred in projects requiring rapid deployment or where technical skills are limited. -
IP Rating (Ingress Protection Rating)
A classification that indicates the degree of protection against dust and water. For LED strips and connectors, IP ratings guide buyers in selecting products suitable for indoor or outdoor use, ensuring compliance with local regulations and environmental conditions.
By mastering these technical properties and trade terms, international B2B buyers can make informed decisions, optimize supply chains, and ensure the successful deployment of LED strip lighting projects across diverse global markets.
Navigating Market Dynamics, Sourcing Trends, and Sustainability in the joining led strips Sector
Market Overview & Key Trends
The joining LED strips sector is experiencing significant growth driven by the global demand for flexible, energy-efficient, and customizable lighting solutions. For international B2B buyers, especially from emerging and developing markets such as Africa, South America, the Middle East, and parts of Europe like Poland and Indonesia, understanding regional market dynamics is crucial. These regions are increasingly investing in infrastructure, commercial spaces, and smart city projects, fueling demand for advanced LED strip solutions that offer seamless connectivity and adaptability.
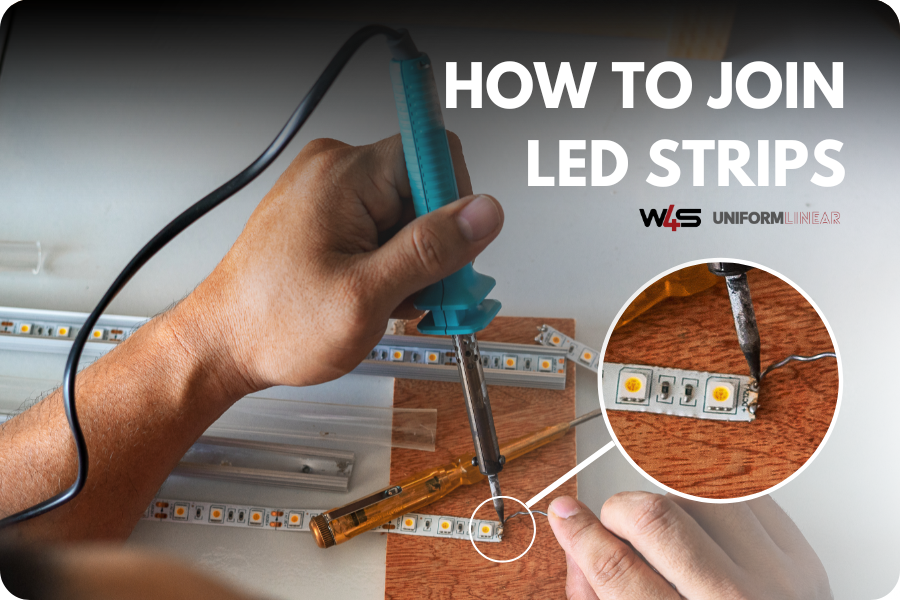
Illustrative Image (Source: Google Search)
Key market drivers include:
- Technological Innovation: Advancements in connectors, soldering-free joint technologies, and modular LED strip designs enhance ease of installation and maintenance, appealing to buyers aiming to reduce labor costs and project timelines.
- Customization & Scalability: The ability to cut and join LED strips at precise points allows for tailored lighting installations, supporting diverse applications from residential and retail to industrial and architectural lighting.
- Supply Chain Diversification: Buyers are increasingly sourcing from multiple regions to mitigate supply disruptions and benefit from competitive pricing, especially with growing manufacturing hubs in Asia and Europe.
- Regulatory Compliance: International standards on electrical safety and quality certification (e.g., CE, RoHS) influence supplier selection, with buyers prioritizing compliant products to ensure market acceptance and reduce liability risks.
For buyers in Africa and South America, localized sourcing partnerships are emerging to address logistical challenges and import costs. The Middle East’s rapid urban development promotes demand for high-quality, durable joining components that can withstand harsh climates. European buyers emphasize innovation and sustainability, often seeking suppliers with transparent supply chains and eco-friendly materials.
Sustainability & Ethical Sourcing in B2B
Sustainability is becoming a critical factor in the procurement of joining LED strips as businesses worldwide align with environmental goals and corporate social responsibility (CSR) commitments. The environmental impact of LED strip production, including raw material extraction (copper, LEDs, plastics), energy consumption, and waste generation, has prompted buyers to seek greener alternatives.
Key considerations for sustainability and ethical sourcing include:
- Material Selection: Opting for joining components made from recycled aluminum or biodegradable plastics reduces environmental footprint. Lead-free solder and halogen-free materials are preferred to minimize toxic emissions.
- Certifications & Standards: Buyers should prioritize suppliers with recognized eco-certifications such as RoHS (Restriction of Hazardous Substances), REACH (Registration, Evaluation, Authorization, and Restriction of Chemicals), and Energy Star compliance to ensure products meet stringent environmental and safety criteria.
- Supply Chain Transparency: Ethical sourcing involves verifying supplier labor practices, ensuring fair wages, and avoiding conflict minerals. B2B buyers increasingly conduct audits or require third-party verifications to uphold ethical standards.
- End-of-Life Management: Considering the recyclability and disposability of joining components contributes to circular economy goals. Modular designs that facilitate disassembly and reuse help reduce electronic waste in large-scale projects.
For international buyers, integrating sustainability criteria into supplier evaluation not only supports global environmental commitments but also enhances brand reputation and compliance with emerging regulations across diverse markets.
Brief Evolution and Historical Context
The joining technology for LED strips has evolved significantly over the past decade. Initially, LED strips were often cut and joined using basic soldering techniques, which required specialized skills and posed risks of poor electrical connections. As demand for LED strip lighting grew across commercial and residential sectors, manufacturers introduced innovative connectors—such as clip-on, snap-fit, and magnetic joins—that simplified installation and improved reliability.
This evolution reflects a broader trend towards modular, plug-and-play lighting solutions that reduce labor costs and installation times. For B2B buyers, understanding this technological progression highlights the importance of selecting joining methods that align with project scale, technical expertise available, and long-term maintenance considerations. Today’s market offers a diverse range of joining options tailored to different voltages, strip widths, and environmental conditions, supporting increasingly complex lighting designs worldwide.
Related Video: International Trade Explained
Frequently Asked Questions (FAQs) for B2B Buyers of joining led strips
-
How can I effectively vet LED strip suppliers for international B2B purchases?
To ensure reliability, verify the supplier’s business license, certifications (e.g., CE, RoHS, UL), and customer reviews. Request samples to test product quality and compatibility with your market’s standards. Engage in direct communication to assess responsiveness and technical knowledge. Utilize third-party inspections or audits, especially for large orders. For buyers in Africa, South America, the Middle East, and Europe, check if the supplier has experience exporting to your region to navigate customs and compliance smoothly. -
What customization options are typically available for joining LED strips, and how do they impact pricing?
Customization can include strip length, LED density, color temperature, waterproofing, connectors, and adhesive backing. Some suppliers also offer branding and packaging customization. These tailored features affect MOQ, lead time, and cost. Bulk customization often reduces unit price but requires higher minimum order quantities. Discuss your project specifications upfront to get accurate quotes and timelines. For international buyers, confirm if customizations meet local regulatory requirements to avoid import issues. -
What are common MOQ and lead times for joining LED strips in international B2B trade?
MOQ varies widely depending on supplier capabilities and customization level, typically ranging from 100 to 1000 meters per order. Lead times usually span 2 to 6 weeks, influenced by product complexity and order volume. For buyers from regions like Indonesia or Poland, factor in additional shipping and customs clearance time. Negotiating flexible MOQs or phased deliveries can help manage inventory and cash flow. Always clarify lead times and penalties for delays before contract signing. -
Which payment terms are standard for international B2B LED strip transactions, and how can buyers protect themselves?
Common payment terms include 30% upfront deposit and 70% balance before shipment or after inspection. Letters of Credit (LC) or escrow services provide added security. For new suppliers, start with smaller orders and use trade assurance platforms when possible. Confirm payment methods accepted (e.g., T/T, PayPal, credit card) and be cautious of upfront full payments without proper due diligence. Clear contract terms regarding refunds, warranties, and dispute resolution are essential.
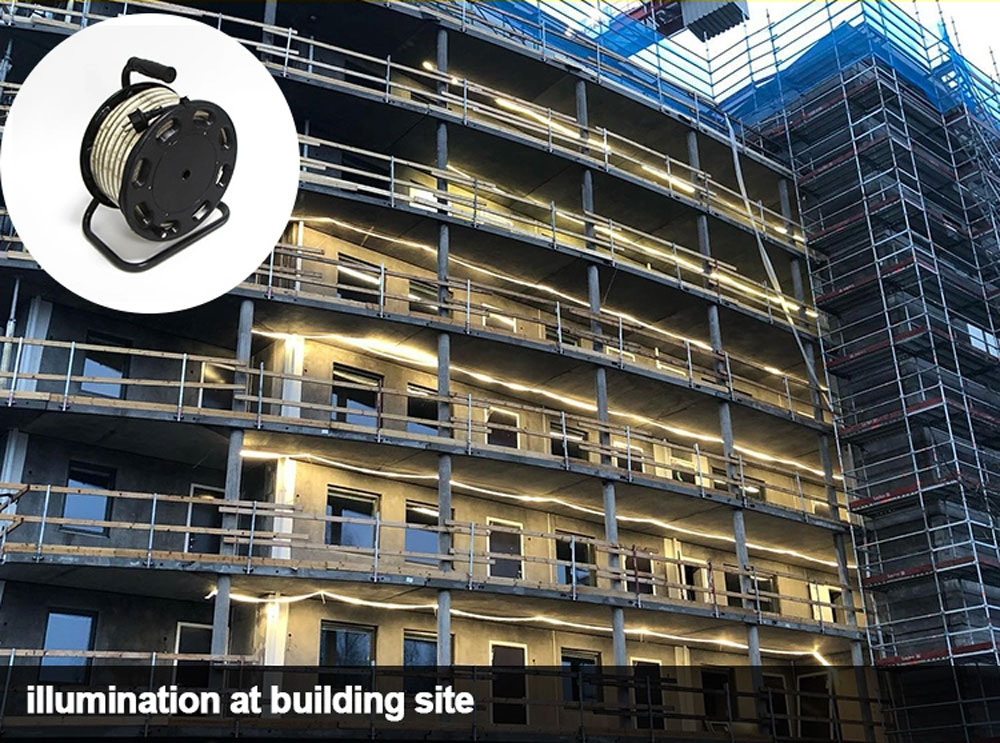
Illustrative Image (Source: Google Search)
-
What quality assurance measures should I expect from reputable LED strip manufacturers?
Reputable manufacturers conduct in-line quality checks, final product testing (e.g., voltage, brightness, waterproof rating), and offer certifications like ISO 9001. Request detailed QA reports and sample batch testing before full production. For international buyers, ensure compliance with local electrical safety standards and environmental regulations. Factory visits or third-party inspections can verify manufacturing processes. Continuous quality monitoring post-shipment, through feedback loops, helps maintain product consistency. -
Which certifications are critical when sourcing joining LED strips for different international markets?
Key certifications include CE (Europe), RoHS (restriction of hazardous substances), UL or ETL (North America), and CCC (China). For Middle Eastern and African markets, look for regional compliance marks and IEC standards. Certifications ensure product safety, electromagnetic compatibility, and environmental compliance, minimizing import and resale risks. Request copies of valid certificates and verify authenticity with issuing bodies. Lack of proper certification can lead to customs seizures or market rejection. -
What logistics considerations should B2B buyers keep in mind when importing joining LED strips?
Understand shipping options (air, sea, express courier) based on cost, volume, and urgency. LED strips are lightweight but often shipped in bulk, so packaging to prevent damage is vital. Confirm Incoterms (FOB, CIF, DDP) to clarify responsibilities and costs. For African and South American buyers, plan for longer transit times and possible customs delays. Partnering with freight forwarders experienced in electronics reduces risk. Always prepare accurate import documentation to avoid clearance issues. -
How should international buyers handle disputes or quality issues after receiving LED strip shipments?
Establish clear contractual terms covering product specifications, inspection rights, and return policies. Document issues with photos and testing reports immediately upon receipt. Communicate promptly with the supplier to seek resolution—partial refunds, replacements, or repair. Use third-party arbitration or trade mediation platforms if direct negotiation fails. Maintaining professional relationships and transparent communication often leads to amicable solutions. For buyers in emerging markets, working with suppliers offering post-sale support is a key advantage.
Important Disclaimer & Terms of Use
⚠️ Important Disclaimer
The information provided in this guide, including content regarding manufacturers, technical specifications, and market analysis, is for informational and educational purposes only. It does not constitute professional procurement advice, financial advice, or legal advice.
While we have made every effort to ensure the accuracy and timeliness of the information, we are not responsible for any errors, omissions, or outdated information. Market conditions, company details, and technical standards are subject to change.
B2B buyers must conduct their own independent and thorough due diligence before making any purchasing decisions. This includes contacting suppliers directly, verifying certifications, requesting samples, and seeking professional consultation. The risk of relying on any information in this guide is borne solely by the reader.
Strategic Sourcing Conclusion and Outlook for joining led strips
Joining LED strips effectively requires a strategic approach that balances technical precision with supply chain considerations. For international B2B buyers, especially those in Africa, South America, the Middle East, and Europe, understanding the nuances of cutting, connecting, and customizing LED strips is essential to meet diverse market demands and project specifications. Prioritizing quality connectors, compatible power supplies, and reliable sourcing channels reduces installation risks and enhances product longevity.
Key takeaways for B2B buyers include:
- Source from reputable manufacturers offering certified components to ensure safety and compliance with regional standards.
- Leverage modular connection solutions such as solderless connectors or clip-on adapters to reduce labor costs and installation time.
- Customize orders based on specific application needs—whether waterproof, flexible, or high-density LED strips—to optimize performance.
- Factor in logistics and after-sales support to ensure seamless supply continuity and technical assistance.
Looking ahead, the LED strip lighting market is poised for growth driven by increasing demand for energy-efficient, customizable lighting solutions in commercial and architectural sectors. Buyers should proactively engage with suppliers who offer innovation in connector technologies and scalable supply capabilities. By doing so, international buyers can capitalize on emerging opportunities, streamline project execution, and deliver superior lighting solutions that cater to evolving client expectations worldwide.