Introduction: Navigating the Global Market for led strip for sewing machine
The integration of LED strips for sewing machines is rapidly becoming a critical factor in enhancing productivity, precision, and operator comfort across global textile and garment manufacturing industries. For international B2B buyers—especially those sourcing from regions like Africa, South America, the Middle East, and Europe—understanding the nuances of LED strip technologies tailored specifically for sewing machines is essential to making smart procurement decisions that drive operational efficiency and reduce downtime.
This comprehensive guide demystifies the global market landscape for LED strips designed for sewing machine applications. It covers a wide spectrum of critical topics including:
- Types and configurations of LED strips optimized for sewing machine illumination
- Key material specifications and durability factors suited for industrial environments
- Insights into manufacturing processes and quality control standards that ensure reliability and long service life
- A curated overview of trusted suppliers and manufacturers across major sourcing regions
- Transparent cost analysis and pricing benchmarks to help assess value and negotiate effectively
- Current market trends and demand drivers impacting supply chain dynamics
- Answers to frequently asked questions addressing installation, compatibility, and maintenance
By synthesizing technical knowledge with practical market intelligence, this guide empowers buyers from diverse international markets—such as textile hubs in the UK, Argentina, and beyond—to confidently evaluate product options and supplier capabilities. The result is a well-informed sourcing strategy that aligns with production goals, budget constraints, and quality expectations, enabling businesses to remain competitive in an evolving global textile manufacturing ecosystem.
Understanding led strip for sewing machine Types and Variations
Type Name | Key Distinguishing Features | Primary B2B Applications | Brief Pros & Cons for Buyers |
---|---|---|---|
24V SMD LED Strip | Surface-mount device LEDs, operates at 24V, flexible design | General sewing machine lighting, workspace illumination | Pros: Low voltage safety, energy efficient, easy to install; Cons: Requires compatible power supply and connectors |
COB LED Strip | Chip-on-board technology, high brightness with uniform light | Precision sewing tasks, detailed workstations | Pros: Superior light uniformity, enhanced brightness; Cons: Higher cost, sensitive to pressure during installation |
RGBW LED Strip | Multi-color LEDs with white channel, dimmable and color adjustable | Customizable lighting setups, mood and task lighting | Pros: Versatile lighting control, supports color customization; Cons: More complex installation, higher initial investment |
Waterproof LED Strip | Encapsulated with silicone or epoxy, resistant to moisture | Industrial sewing environments, outdoor or humid locations | Pros: Durable in harsh conditions, long lifespan; Cons: Slightly bulkier, potentially higher price |
Rigid Aluminum Profile LED Strip | Mounted on aluminum channel for heat dissipation and protection | Heavy-duty sewing machines, professional workshops | Pros: Enhanced cooling, mechanical protection; Cons: Less flexible, installation may require more effort |
24V SMD LED Strip
This is the most common type used for sewing machines due to its flexibility and safety profile. Operating at 24 volts DC reduces electrical hazards, making it suitable for various international markets including Africa and South America where safety standards are critical. B2B buyers should prioritize compatibility with power supplies and connectors to ensure seamless integration. The strips are energy efficient and easy to install, ideal for general-purpose illumination in sewing workshops.
COB LED Strip
Featuring chip-on-board technology, COB strips deliver a highly uniform and intense light output, which is essential for detailed sewing tasks requiring precision. These strips are favored in professional tailoring and manufacturing environments across Europe and the Middle East. Buyers should note the sensitivity of COB strips to mechanical pressure during installation, requiring careful handling and potentially higher upfront costs balanced by superior lighting performance.
RGBW LED Strip
RGBW strips combine color-changing RGB LEDs with an additional white LED channel, allowing for adjustable color temperatures and dimming options. This versatility is advantageous for bespoke sewing operations or high-end fashion production where lighting ambiance can impact quality control. B2B buyers must consider the complexity of installation and control systems, as well as the need for compatible dimmers or smart controls, which may increase investment but add significant value.
Waterproof LED Strip
Designed with silicone or epoxy encapsulation, waterproof LED strips are suitable for sewing environments exposed to moisture, such as industrial workshops or outdoor tailoring stations common in certain African and Middle Eastern markets. These strips offer enhanced durability and longevity but may be bulkier and costlier than non-waterproof variants. Buyers should evaluate environmental conditions carefully to justify this investment.
Rigid Aluminum Profile LED Strip
These LED strips are integrated into aluminum channels that provide efficient heat dissipation and robust mechanical protection. They are ideal for heavy-duty sewing machines and professional workshop settings in Europe and South America where reliability and longevity are paramount. While installation may be more involved and less flexible, the enhanced cooling extends LED lifespan, offering excellent long-term value for bulk purchasers.
Related Video: How to Install the LED Sewing Machine Light
Key Industrial Applications of led strip for sewing machine
Industry/Sector | Specific Application of led strip for sewing machine | Value/Benefit for the Business | Key Sourcing Considerations for this Application |
---|---|---|---|
Textile & Garment Factories | Integrated task lighting on industrial sewing machines | Enhances operator precision and reduces eye strain, improving product quality and reducing errors | Durable, heat-resistant LED strips with consistent brightness and easy installation in diverse factory environments |
Automotive Upholstery | Illumination of stitching areas on automotive seat and interior fabric production | Enables detailed stitching in low-light conditions, ensuring high-quality finish and compliance with safety standards | Waterproof and vibration-resistant LED strips suitable for automotive production lines and harsh environments |
Footwear Manufacturing | Focused lighting on stitching zones for leather and fabric shoe assembly | Improves seam accuracy and reduces defects, increasing throughput and lowering rework costs | Flexible LED strips that conform to machine shapes and withstand dust and humidity common in footwear plants |
Home Furnishing & Upholstery | Task-specific lighting for sewing upholstery fabrics and decorative stitching | Facilitates intricate decorative stitching and pattern matching, boosting product appeal and reducing waste | Energy-efficient LED strips with adjustable brightness to adapt to various fabric types and operator preferences |
Apparel Design & Prototyping | Adjustable LED lighting on sewing machines for sample making and design development | Allows designers to work with fine details and color matching under optimal lighting, accelerating prototyping cycles | Compact, low-heat LED strips with dimming capabilities and easy retrofit options for varied sewing machine models |
Industrial sewing environments benefit significantly from the integration of LED strips on sewing machines, offering enhanced task lighting that directly improves operator efficiency and product quality. In textile and garment factories, LED strips provide consistent, bright illumination that reduces eye strain and helps operators detect stitching errors early. For international buyers in regions such as Africa and South America, sourcing LED strips that can withstand high temperatures and humidity is critical to maintaining long-term performance.
In automotive upholstery production, precise lighting on sewing machines is essential to meet stringent quality and safety standards. LED strips that are waterproof and vibration-resistant ensure reliable operation in automotive manufacturing plants, which often experience harsh conditions. Buyers from the Middle East and Europe should focus on LED strips certified for industrial use and compatible with existing machine setups.
Footwear manufacturers require flexible LED strips that conform to the irregular shapes of sewing machines used for leather and fabric assembly. These LED strips must resist dust and moisture typical in shoe production environments. For B2B buyers in emerging markets like Africa or Argentina, durability and ease of installation are key factors to reduce downtime and maintenance costs.
The home furnishing and upholstery sector uses LED strips to illuminate sewing tasks involving decorative stitching and fabric pattern alignment. Energy-efficient LEDs with adjustable brightness allow operators to tailor lighting to different fabric textures and colors. International buyers should prioritize LED strips with dimming options and robust adhesive backing to ensure stable mounting on various sewing machine models.
In apparel design and prototyping, adjustable LED lighting supports detailed sample making and color matching, speeding up design iterations. Compact, low-heat LED strips with dimming functionality are preferred to prevent heat damage to delicate fabrics and allow flexible lighting setups. Buyers from all regions should seek LED solutions that are easy to retrofit and compatible with diverse sewing machine brands commonly used in design studios.
Related Video: How To: Use an Industrial Sewing Machine
Strategic Material Selection Guide for led strip for sewing machine
When selecting materials for LED strips designed specifically for sewing machines, international B2B buyers must consider factors such as durability under mechanical stress, heat dissipation, corrosion resistance, and compliance with regional standards. The choice of material directly influences the product’s performance, longevity, and compatibility with various industrial environments prevalent in Africa, South America, the Middle East, and Europe.
Aluminium
Key Properties: Aluminium is widely used for LED strip profiles due to its excellent thermal conductivity, lightweight nature, and corrosion resistance. It typically withstands temperatures up to 150°C and offers good mechanical strength, essential for protecting delicate LED components on sewing machines.
Pros & Cons: Aluminium profiles enhance heat dissipation, which extends LED lifespan—critical in continuous industrial sewing operations. They are relatively easy to machine and form, allowing for customized profiles. However, aluminium can be more costly than plastic alternatives and may require anodizing or powder coating to improve surface durability and corrosion resistance in humid or salty environments.
Impact on Application: Aluminium’s superior heat management makes it ideal for sewing machines operating in hot climates or under heavy use, such as in textile factories across Brazil or the UAE. Its corrosion resistance suits regions with high humidity or coastal exposure, such as parts of South Africa or Argentina.
International Considerations: Aluminium profiles generally comply with ASTM B221 (USA), DIN 1748 (Germany), and JIS H4000 (Japan) standards, which are recognized globally. Buyers in Europe and the Middle East should verify anodizing quality to meet local corrosion resistance requirements. In Africa and South America, sourcing anodized aluminium locally may reduce costs and lead times.
Polycarbonate (PC)
Key Properties: Polycarbonate is a durable thermoplastic with high impact resistance, good heat tolerance (up to about 115°C), and excellent optical clarity. It also offers good electrical insulation, which is advantageous for LED strip safety.
Pros & Cons: PC is lightweight, easy to mold into complex shapes, and resistant to shattering, making it suitable for protective covers on sewing machine LED strips. However, it has lower thermal conductivity compared to metals, which may reduce heat dissipation efficiency. It can yellow over time under UV exposure unless treated.
Impact on Application: Polycarbonate is suitable for sewing machines used in environments where impact resistance is critical, such as busy garment workshops in Nigeria or Argentina. Its electrical insulation properties enhance operator safety. However, in high-temperature industrial settings, additional cooling solutions may be necessary.
International Considerations: Polycarbonate materials often meet ISO 178 and ASTM D638 standards for mechanical properties. Buyers from Europe and the Middle East should ensure UV stabilization additives are included for longevity. In Africa and South America, the availability of UV-resistant PC grades varies, so specifying this upfront is crucial.
Silicone (for flexible LED strip coatings)
Key Properties: Silicone offers excellent flexibility, high temperature resistance (up to 200°C), and outstanding resistance to moisture, chemicals, and UV radiation. It is commonly used as a protective coating or encapsulant for flexible LED strips.
Pros & Cons: Silicone coatings protect LED strips from dust, oils, and mechanical abrasion common in sewing environments. They maintain flexibility, which is vital for LED strips that must bend around machine contours. The downside is a higher material cost and more complex application processes.
Impact on Application: Silicone-coated LED strips are ideal for sewing machines exposed to oily or dusty conditions, such as leather workshops in Morocco or textile factories in Turkey. The flexibility supports installation on curved surfaces, enhancing lighting uniformity.
International Considerations: Silicone materials typically comply with ASTM D2000 and ISO 10993 for chemical and temperature resistance. Buyers in Europe and the Middle East benefit from certifications related to RoHS and REACH compliance. In African and South American markets, verifying local chemical safety standards and ensuring supplier traceability is recommended.
Copper (for LED strip circuitry and connectors)
Key Properties: Copper is primarily used in the LED strip’s flexible printed circuit boards (FPCBs) and connectors due to its excellent electrical conductivity and moderate thermal conductivity. Copper layers typically range from 35µm to 105µm thickness.
Pros & Cons: Copper ensures efficient power delivery and heat dissipation within the LED strip, improving brightness and reliability. It is relatively cost-effective but prone to oxidation if not properly coated or sealed, which can degrade performance.
Impact on Application: High-quality copper circuitry is essential for sewing machines requiring stable, flicker-free lighting, especially in precision stitching tasks common in European and Middle Eastern manufacturing. In humid or corrosive environments like coastal regions in South America or Africa, protective coatings are critical.
International Considerations: Copper used in LED strips should meet IPC-6012 standards for PCB quality and IEC 60228 for conductor purity. Buyers should confirm that suppliers provide oxidation-resistant coatings compliant with regional environmental regulations, especially in markets with strict import controls like the UK and EU.
Material | Typical Use Case for led strip for sewing machine | Key Advantage | Key Disadvantage/Limitation | Relative Cost (Low/Med/High) |
---|---|---|---|---|
Aluminium | LED strip housing/profile for heat dissipation and mechanical protection | Excellent heat dissipation and corrosion resistance | Higher cost and requires surface treatment | Medium |
Polycarbonate | Protective covers and diffusers for impact resistance and insulation | High impact resistance and electrical insulation | Lower thermal conductivity and potential yellowing | Medium |
Silicone | Flexible protective coating for LED strips in harsh environments | High temperature and chemical resistance, flexibility | Higher material and application cost | High |
Copper | Conductive layers in flexible PCBs and connectors | Superior electrical and thermal conductivity | Susceptible to oxidation without proper coating | Medium |
In-depth Look: Manufacturing Processes and Quality Assurance for led strip for sewing machine
Manufacturing Processes of LED Strips for Sewing Machines
The production of LED strips designed specifically for sewing machines involves several precise manufacturing stages to ensure durability, optimal lighting performance, and compatibility with industrial sewing environments.
1. Material Preparation
This initial phase focuses on sourcing and preparing high-quality raw materials:
- LED Chips and Substrate: High-efficiency SMD (Surface-Mount Device) LEDs or COB (Chip-on-Board) LEDs are commonly used. The substrate, often a flexible PCB (Printed Circuit Board) with copper layers, is selected for excellent thermal conductivity.
- Adhesives and Encapsulation Materials: Specialized adhesives with strong bonding and heat resistance are prepared, alongside silicone or epoxy encapsulants that protect LEDs from dust, moisture, and mechanical stress.
- Connectors and Wiring: Reliable connectors and copper wiring, compliant with low-voltage safety standards (typically 12V or 24V DC), are prepped for assembly.
2. Forming and Assembly
Key techniques here include precision mounting, soldering, and encapsulation:
- Automated SMT (Surface Mount Technology) Placement: LEDs are mounted on the flexible PCB with high accuracy to ensure consistent light distribution and electrical connectivity.
- Soldering: Both wave soldering and reflow soldering are used, depending on the LED type, ensuring strong and reliable electrical joints.
- Cutting and Shaping: The LED strips are cut to standardized lengths suitable for sewing machine integration, with designated cut points to maintain functionality.
- Encapsulation and Coating: Protective layers are applied to shield against vibrations, dust, and humidity typical in sewing environments. UV-resistant coatings may be added for longevity.
- Attachment Features: Backing adhesives (often 3M-type tapes) or aluminum profiles for heat dissipation and mechanical protection are applied.
3. Finishing Processes
The finishing touches ensure ease of installation and operational safety:
- Quality Markings: Each strip is labeled with voltage, wattage, and polarity markings for easy identification.
- Connector Installation: Plug-and-play connectors or terminal blocks are attached for seamless integration into sewing machine electrical systems.
- Packaging: Anti-static and moisture-resistant packaging is used to protect strips during transport.
Quality Assurance and Control (QA/QC) in LED Strip Production
Robust quality assurance protocols are critical to guarantee that LED strips meet international standards and the demanding operational conditions of sewing machines.
Relevant International and Industry Standards
- ISO 9001: Ensures comprehensive quality management systems are in place throughout manufacturing.
- CE Marking: Mandatory for products sold within the European Economic Area, indicating compliance with safety, health, and environmental requirements.
- RoHS (Restriction of Hazardous Substances): Confirms that LED strips are free from harmful materials like lead and mercury.
- UL and IEC Standards: Safety certifications relevant in various global markets, ensuring electrical safety and performance.
- Industry-Specific Standards: In some regions, additional certifications such as API (American Petroleum Institute) may be required if the sewing machines are used in specialized industries (e.g., protective clothing manufacturing).
Key QC Checkpoints
-
Incoming Quality Control (IQC):
– Inspection of raw materials including LED chips, PCBs, adhesives, and connectors.
– Verification of certificates of conformity from suppliers. -
In-Process Quality Control (IPQC):
– Monitoring of SMT placement accuracy via automated optical inspection (AOI).
– Solder joint integrity checks through X-ray or visual inspection.
– Adhesive application consistency and curing process verification.
– Functional testing of LED segments for uniform brightness and color. -
Final Quality Control (FQC):
– Complete electrical testing under operational voltages to detect shorts, open circuits, or flickering.
– Environmental stress tests such as thermal cycling and humidity exposure to simulate sewing machine operating conditions.
– Adhesion tests for backing tape and encapsulants.
– Dimensional and visual inspection to ensure proper finishing and marking.
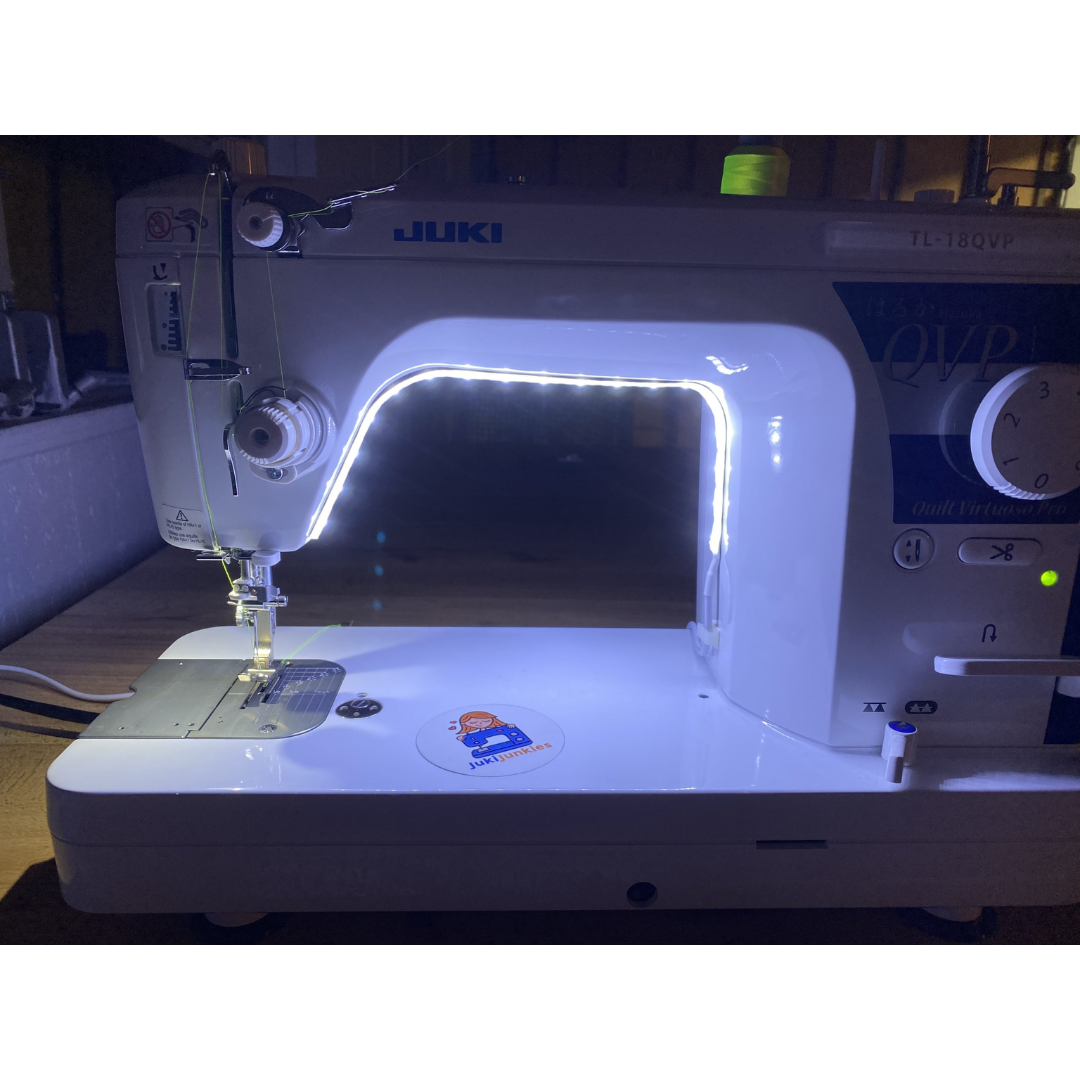
Illustrative Image (Source: Google Search)
Common Testing Methods
- Electrical Testing: Using specialized LED testers to check voltage, current consumption, and luminous intensity.
- Thermal Imaging: Identifies hotspots that could reduce lifespan or cause failure.
- Accelerated Aging Tests: Simulate long-term usage to detect early failures.
- Mechanical Stress Testing: Ensures strips withstand vibrations and bending during sewing machine operation.
- Adhesion and Peel Tests: Confirm strong and durable bonding of adhesive layers.
Verifying Supplier Quality: Best Practices for International B2B Buyers
For buyers in Africa, South America, the Middle East, and Europe, ensuring supplier QC adherence is crucial to secure reliable, high-performance LED strips.
- Factory Audits: Conduct on-site or third-party audits focusing on manufacturing capabilities, process controls, and quality management systems.
- Reviewing Quality Documentation: Request ISO 9001 certificates, CE declarations, RoHS compliance reports, and detailed QC test reports.
- Third-Party Inspections: Employ independent inspection agencies to verify product conformity before shipment.
- Sample Testing: Order samples for in-house or third-party laboratory testing under your specific operational conditions.
- Supplier Transparency: Prioritize suppliers who provide full traceability of materials and processes.
QC and Certification Nuances for Different Regions
-
Africa and South America:
Buyers should be aware of possible import regulations and certification recognition. CE marking is often accepted, but additional local certifications may be required. It is advisable to verify compliance with local electrical safety standards and customs requirements. -
Middle East:
Compliance with Gulf Cooperation Council (GCC) standards and safety certifications like SASO (Saudi Standards) may be necessary alongside CE and RoHS. Suppliers with experience exporting to these markets can navigate these complexities more effectively. -
Europe (including UK):
Post-Brexit, UK buyers should ensure products carry UKCA marking if CE is not accepted. Strict adherence to EU directives (such as RoHS and REACH) remains essential for mainland Europe. Buyers often demand rigorous documentation and traceability.
Summary for B2B Buyers
Understanding the manufacturing and quality assurance processes behind LED strips for sewing machines empowers international buyers to make informed sourcing decisions. Focus on suppliers demonstrating:
- Advanced manufacturing capabilities with automated SMT and robust assembly lines.
- Comprehensive QC systems aligned with international standards (ISO 9001, CE, RoHS).
- Transparent and verifiable quality documentation and inspection options.
- Experience in exporting to your regional market, ensuring compliance with local regulations.
This strategic approach reduces risks, ensures product reliability, and supports long-term partnerships in global B2B trade.
Related Video: Inside LEDYi LED Strip Factory | Full Manufacturing Process by Leading LED Strip Manufacturer
Comprehensive Cost and Pricing Analysis for led strip for sewing machine Sourcing
Understanding Cost Components in LED Strip Sourcing for Sewing Machines
When sourcing LED strips tailored for sewing machine applications, it is crucial to dissect the cost structure thoroughly. The primary cost components include:
-
Materials: This accounts for the LED chips (commonly 24V SMD or COB types), flexible PCB substrates, adhesives, connectors, and protective profiles (often aluminum for heat dissipation). High-quality materials with certifications (e.g., RoHS, CE) typically command higher prices but ensure durability and compliance.
-
Labor: Skilled labor is involved in assembly, soldering, quality checks, and packaging. Labor costs vary significantly by country and affect the final price, especially for customized or small-batch orders.
-
Manufacturing Overhead: Includes factory utilities, equipment depreciation, and indirect labor. Efficient factories with modern automation can reduce overhead, improving cost competitiveness.
-
Tooling: Initial tooling costs for custom LED strip designs or connectors can be substantial. These are amortized over production volume, impacting pricing more for low MOQ orders.
-
Quality Control (QC): Rigorous QC processes, including electrical testing and visual inspections, add to the cost but are vital for reliable operation in industrial sewing environments.
-
Logistics: Shipping, customs duties, and insurance costs vary by destination. For buyers in Africa, South America, the Middle East, and Europe, these costs can fluctuate based on port infrastructure and freight options (sea, air, or courier).
-
Margin: Supplier markup depends on brand positioning, service level, and market demand. Established suppliers with strong reputations may price higher but offer greater reliability.
Key Price Influencers Impacting LED Strip Procurement
Several factors influence the quoted prices from LED strip manufacturers:
-
Order Volume and Minimum Order Quantity (MOQ): Larger volumes reduce per-unit cost via economies of scale. Suppliers often set MOQs to justify tooling and setup costs. International buyers should balance MOQ with warehouse capacity and demand forecasts.
-
Specifications and Customization: Custom lengths, specific LED densities, color temperatures, waterproofing, or integrated dimming features increase complexity and cost. Standardized products are more cost-effective but may require compromises on functionality.
-
Material Quality and Certifications: Premium LEDs, aluminum profiles, and certified components ensure longevity and safety, raising costs but reducing Total Cost of Ownership (TCO) through less frequent replacements.
-
Supplier Location and Reliability: Manufacturers in Asia typically offer lower prices but may involve longer lead times and higher shipping costs. European suppliers may charge premiums but provide faster delivery and easier communication.
-
Incoterms and Payment Terms: The choice of Incoterms (e.g., FOB, CIF, DDP) affects who bears shipping and customs risks. Buyers should clarify these terms upfront to avoid unexpected expenses.
Strategic Buyer Tips for International B2B Procurement
For international buyers from Africa, South America, the Middle East, and Europe, adopting a strategic approach to cost and pricing negotiation can unlock significant savings and quality assurance:
-
Negotiate Based on Total Cost of Ownership: Don’t focus solely on unit price. Factor in installation ease, energy consumption, lifespan, and after-sales support. For example, a higher upfront cost for an LED strip with better heat dissipation and certified power supplies can reduce downtime and maintenance costs.
-
Leverage Volume Consolidation: Coordinate with other sewing machine manufacturers or distributors in your region to aggregate orders, thus accessing better pricing tiers and reducing freight costs per unit.
-
Assess Supplier Capabilities and Certifications: Prioritize suppliers who demonstrate compliance with international standards and can provide test reports. This reduces risks of product failures or regulatory issues in your market.
-
Understand Pricing Nuances by Region: Shipping to remote or less accessible ports can add significant costs. Consider suppliers with local warehouses or those offering DDP terms to simplify import processes and avoid hidden charges.
-
Request Transparent Cost Breakdowns: Engage suppliers to provide itemized quotes detailing material, labor, and logistics costs. This transparency allows better negotiation leverage and identification of cost-saving opportunities.
-
Plan for Currency Fluctuations and Payment Terms: Especially relevant for buyers in emerging markets, negotiating fixed exchange rates or flexible payment terms can protect against volatile currency impacts.
Indicative Pricing Disclaimer
Prices for LED strips designed for sewing machines vary widely based on specifications, order size, and sourcing region. As a rough benchmark, standard 24V LED strips with aluminum profiles and basic connectors may range from $5 to $15 per meter at medium volumes (hundreds to thousands of meters). Custom or high-spec variants with integrated dimming or waterproofing can exceed $20 per meter. Logistics and import duties add further costs depending on destination. Buyers should obtain tailored quotations reflecting their exact requirements and delivery terms.
By comprehensively analyzing these cost factors and negotiating strategically, international B2B buyers can optimize their sourcing of LED strips for sewing machines, balancing quality, reliability, and price to suit their markets in Africa, South America, the Middle East, and Europe.
Spotlight on Potential led strip for sewing machine Manufacturers and Suppliers
This section looks at several manufacturers active in the ‘led strip for sewing machine’ market. This is a representative sample for illustrative purposes; B2B buyers must conduct extensive due diligence before any transaction. Information is synthesized from public sources and general industry knowledge.
Essential Technical Properties and Trade Terminology for led strip for sewing machine
Critical Technical Properties of LED Strips for Sewing Machines
When sourcing LED strips for sewing machines, understanding key technical specifications ensures product reliability, safety, and optimal performance in industrial environments. Below are essential properties that international B2B buyers should prioritize:
-
Voltage and Power Rating (Typically 12V or 24V DC):
LED strips designed for sewing machines commonly operate on low voltage (12V or 24V DC). This low-voltage operation is crucial for safety, especially in textile manufacturing where moisture and human contact are concerns. Correct voltage ensures compatibility with existing power supplies and prevents premature failure. -
LED Chip Type and Density:
The type of LED chips (e.g., SMD 2835, 5050, COB) and their density per meter affect brightness and uniformity. Higher density and advanced chip types provide consistent illumination crucial for detailed sewing work. For B2B buyers, selecting the right chip type influences energy efficiency and maintenance intervals. -
Material Quality and Heat Dissipation:
The base material, often flexible PCB coated with copper, must have high thermal conductivity to dissipate heat effectively. Aluminum profiles or heat sinks are frequently used to extend LED lifespan. Overheating can reduce LED life, so buyers should verify material grades and cooling solutions to ensure durability. -
IP Rating (Ingress Protection):
Depending on the sewing environment, LED strips may require protection against dust, oils, and occasional moisture (e.g., IP20, IP65). An appropriate IP rating guarantees operational stability in factory conditions and prevents damage from contaminants. -
Cutting and Connection Flexibility:
LED strips should support customizable lengths with clearly marked cutting points and reliable connectors or soldering options. This flexibility allows seamless integration into various sewing machine models and layouts, minimizing installation time and complexity. -
Color Temperature and CRI (Color Rendering Index):
For precision sewing, LED strips with neutral to cool white color temperatures (4000K to 6000K) are preferred as they provide clear visibility without color distortion. A high CRI (above 80) ensures accurate color perception of fabrics, which is vital for quality control.
Common Trade Terminology for LED Strip Procurement
Understanding industry jargon empowers buyers to navigate supplier communications and contracts effectively. Here are key terms frequently encountered in B2B LED strip transactions:
-
OEM (Original Equipment Manufacturer):
Refers to suppliers who produce LED strips that can be branded and customized according to the buyer’s specifications. OEM partnerships allow sewing machine manufacturers to integrate lighting solutions tailored to their product design and branding needs. -
MOQ (Minimum Order Quantity):
The smallest quantity a supplier is willing to sell in one order. MOQ impacts inventory planning and cost efficiency, especially for startups or smaller sewing machine manufacturers. Negotiating MOQ can optimize capital expenditure and reduce storage requirements. -
RFQ (Request for Quotation):
A formal inquiry sent by buyers to suppliers asking for detailed pricing, specifications, and delivery terms. RFQs are essential for comparing offers and selecting the best supplier based on cost, quality, and service. -
Incoterms (International Commercial Terms):
Standardized trade terms defining responsibilities for shipping, insurance, and customs clearance between buyers and sellers. Common Incoterms include FOB (Free On Board) and CIF (Cost, Insurance, and Freight). Clear understanding prevents disputes and clarifies cost allocation. -
Lead Time:
The time from order confirmation to product delivery. Accurate lead time estimates are critical for production scheduling and meeting market demand without delays. -
Dimming and Control Compatibility:
Refers to the LED strip’s ability to be integrated with dimmers or controllers (e.g., PWM dimming). This feature is important for sewing machines requiring adjustable lighting intensity to reduce eye strain or adapt to different fabric types.
By focusing on these technical properties and trade terms, B2B buyers from Africa, South America, the Middle East, and Europe can make informed purchasing decisions that align with their operational requirements and market expectations. This knowledge also supports effective supplier negotiations, ensuring quality, compliance, and cost-effectiveness in LED strip procurement for sewing machines.
Navigating Market Dynamics, Sourcing Trends, and Sustainability in the led strip for sewing machine Sector
Market Overview & Key Trends
The global market for LED strips designed specifically for sewing machines is experiencing steady growth driven by increasing automation and precision demands in the textile and garment manufacturing sectors. For international B2B buyers, especially those in Africa, South America, the Middle East, and Europe (such as the UK and Argentina), the appeal lies in enhanced operational efficiency, improved visibility, and energy savings. As sewing machines become more sophisticated, integrated LED lighting solutions are no longer optional but essential for quality control and operator comfort.
Key market drivers include the shift towards low-voltage (typically 24V) LED strips that offer safer operation and compatibility with advanced dimming controls. Buyers are increasingly sourcing LED strips with modular connectors and profiles that facilitate easy installation, maintenance, and scalability. The availability of flexible, high-brightness SMD and COB LED strips enables customization to fit diverse sewing machine models and workspace layouts, meeting the demand for ergonomic and adaptable lighting.
Emerging trends highlight a move toward smart LED solutions with wireless dimming and color temperature adjustment, allowing manufacturers to optimize lighting conditions for various fabric types and sewing tasks. From a sourcing perspective, international buyers prioritize suppliers offering comprehensive accessory kits—power supplies, connectors, profiles, and controllers—to simplify procurement and reduce lead times. Regional differences in supplier capabilities and logistical infrastructure mean buyers must carefully evaluate total cost of ownership, including shipping, customs, and after-sales support.
Furthermore, the increasing digitization of supply chains and adoption of traceability technologies empower buyers to vet suppliers rigorously. This is particularly relevant for markets in Africa and South America, where reliable sourcing partnerships can mitigate risks of counterfeit or substandard components. European and Middle Eastern buyers often seek compliance with stringent safety and quality standards, which influences supplier selection and contract negotiations.
Sustainability & Ethical Sourcing in B2B
Sustainability is rapidly becoming a critical consideration in sourcing LED strips for sewing machines. The textile industry’s environmental footprint has drawn global scrutiny, pushing manufacturers and suppliers to adopt greener lighting solutions. For B2B buyers, selecting LED strips manufactured with eco-friendly materials and processes can significantly reduce energy consumption and carbon emissions in production facilities.
Ethical sourcing is equally vital. Buyers are increasingly demanding transparency regarding the origin of raw materials, labor conditions, and supplier environmental policies. Certifications such as RoHS (Restriction of Hazardous Substances), REACH (Registration, Evaluation, Authorization, and Restriction of Chemicals), and ISO 14001 (Environmental Management) serve as important benchmarks for verifying compliance and minimizing toxic substances in LED components. These certifications assure buyers in Europe, the Middle East, and beyond that products meet high environmental and safety standards.
Additionally, aluminum profiles used for LED strip mounting are often recycled or sourced from suppliers committed to sustainable mining practices. The use of low-voltage power supplies further reduces energy waste and enhances workplace safety. Buyers should also consider suppliers that offer take-back or recycling programs for end-of-life LED strips to support circular economy initiatives.
From a practical standpoint, integrating sustainability into procurement policies helps businesses meet corporate social responsibility (CSR) goals and regulatory requirements in their home markets. It also strengthens brand reputation among increasingly eco-conscious customers and partners. For regions such as Africa and South America, adopting sustainable sourcing practices can foster long-term supplier relationships and open access to international markets with strict environmental mandates.
Brief Evolution of LED Strips for Sewing Machines
LED lighting integration in sewing machines evolved from basic illumination solutions aimed at improving operator visibility to sophisticated, modular systems tailored for industrial applications. Early adoption focused on standard fluorescent or incandescent bulbs, which had limitations in energy efficiency and heat generation. The transition to LED strips began in the early 2000s, driven by advances in surface-mount device (SMD) technology and the miniaturization of electronic components.
Over time, manufacturers introduced low-voltage LED strips with adhesive backing, flexible designs, and aluminum profiles to address installation challenges and durability concerns. The emergence of COB (Chip on Board) LED strips further enhanced brightness and uniformity, ideal for detailed sewing work. Today’s LED strips often feature smart controls compatible with factory automation systems, reflecting a broader industry trend towards digital transformation and sustainability. This evolution has enabled B2B buyers to leverage lighting as a key factor in improving sewing machine performance and operator ergonomics across diverse global markets.
Related Video: Incoterms for beginners | Global Trade Explained
Frequently Asked Questions (FAQs) for B2B Buyers of led strip for sewing machine
-
How can I effectively vet suppliers of LED strips for sewing machines to ensure quality and reliability?
To vet suppliers, request detailed product specifications, certifications (e.g., CE, RoHS, UL), and quality assurance processes. Ask for samples to test performance and durability, particularly heat dissipation and adhesion properties critical for sewing machine environments. Verify references or customer reviews, focusing on international trade experience and after-sales support. Conduct factory audits or third-party inspections when possible. Prioritize suppliers with transparent communication and proven export logistics, especially those accustomed to serving markets in Africa, South America, the Middle East, and Europe. -
What customization options are typically available for LED strips used in sewing machines?
Most manufacturers offer customization including strip length, LED density, color temperature, voltage (commonly 12V or 24V), and adhesive backing type. You can also request specific IP ratings for moisture resistance or aluminum profiles for heat dissipation. Custom connectors or dimming capabilities compatible with sewing machine controls are often possible. Discuss your exact sewing machine model and operating conditions with suppliers to ensure the LED strips meet your functional and installation requirements. -
What are common minimum order quantities (MOQs) and lead times for international orders of LED strips for sewing machines?
MOQs vary widely, typically ranging from 100 to 500 meters per order for customized LED strips. Standard products may have lower MOQs. Lead times generally span 3 to 8 weeks depending on customization complexity, supplier capacity, and shipping methods. For buyers in regions like Africa or South America, account for additional transit time and customs clearance. Early communication with suppliers to clarify MOQs and production schedules is essential to align with your supply chain needs. -
Which payment terms are standard in international B2B transactions for LED strips, and how can I protect my investment?
Common payment terms include 30% deposit upfront and 70% balance before shipment or upon delivery. Letters of credit (LC) and escrow services provide added security for larger orders. Ensure contracts specify quality standards, delivery timelines, and penalties for non-compliance. Using trade assurance platforms or escrow accounts can mitigate risks. Confirm supplier bank details independently to avoid fraud, and consider payment insurance options, especially when dealing with new suppliers in emerging markets. -
What quality assurance certifications should I look for when sourcing LED strips for sewing machines?
Look for international certifications such as CE (European conformity), RoHS (restriction of hazardous substances), UL (safety in the US), and ISO 9001 (quality management). These indicate compliance with safety, environmental, and quality standards. Certifications related to electrical safety and electromagnetic compatibility are particularly important. Suppliers should provide test reports for lumen output, durability, and heat resistance. Request batch testing documentation and inquire about their in-house quality control processes to ensure consistent product performance. -
How should I plan logistics and shipping for LED strip orders to regions like Africa, South America, or the Middle East?
Choose suppliers experienced in international shipping with options for air freight (faster but costlier) or sea freight (cost-effective for bulk). Confirm Incoterms (e.g., FOB, CIF) to clarify responsibilities. Be aware of import regulations, customs duties, and potential delays specific to your country. Packaging should protect LED strips from moisture and mechanical damage. Collaborate with freight forwarders familiar with your destination to optimize transit routes and costs. Early planning helps avoid supply chain disruptions. -
What are best practices for resolving disputes or quality issues with international LED strip suppliers?
Maintain clear documentation including contracts, specifications, and communication records. If quality issues arise, request photographic or video evidence and product samples. Engage suppliers promptly to negotiate solutions such as replacement shipments, refunds, or discounts. Utilize third-party inspection or arbitration if necessary. Establish dispute resolution clauses in contracts specifying jurisdiction and legal recourse. Building strong relationships and open communication with suppliers often helps prevent conflicts and facilitates quicker resolution. -
Are there specific considerations for LED strips used in sewing machines in different climates or regions?
Yes, environmental factors like humidity, temperature fluctuations, and dust vary by region and affect LED strip performance. For humid or hot climates (e.g., Middle East, parts of Africa), opt for LED strips with higher IP ratings and aluminum profiles for heat dissipation. In dusty or abrasive environments, protective covers or profiles help prolong lifespan. Discuss regional conditions with suppliers to select appropriate adhesives and materials. Proper installation and maintenance tailored to local conditions ensure reliable operation and longevity.
Important Disclaimer & Terms of Use
⚠️ Important Disclaimer
The information provided in this guide, including content regarding manufacturers, technical specifications, and market analysis, is for informational and educational purposes only. It does not constitute professional procurement advice, financial advice, or legal advice.
While we have made every effort to ensure the accuracy and timeliness of the information, we are not responsible for any errors, omissions, or outdated information. Market conditions, company details, and technical standards are subject to change.
B2B buyers must conduct their own independent and thorough due diligence before making any purchasing decisions. This includes contacting suppliers directly, verifying certifications, requesting samples, and seeking professional consultation. The risk of relying on any information in this guide is borne solely by the reader.
Strategic Sourcing Conclusion and Outlook for led strip for sewing machine
Optimizing Procurement for LED Strips in Sewing Machines: Key Insights and Future Directions
For international B2B buyers in Africa, South America, the Middle East, and Europe, sourcing high-quality LED strips tailored for sewing machines requires a strategic approach emphasizing reliability, compatibility, and supplier expertise. Prioritize suppliers who offer comprehensive solutions, including 24V low-voltage strips, robust power supplies, and versatile connectors that ensure safe, efficient, and durable integration with industrial sewing equipment. Attention to product specifications such as heat dissipation via aluminum profiles and ease of installation through strong adhesive backing can significantly reduce downtime and maintenance costs.
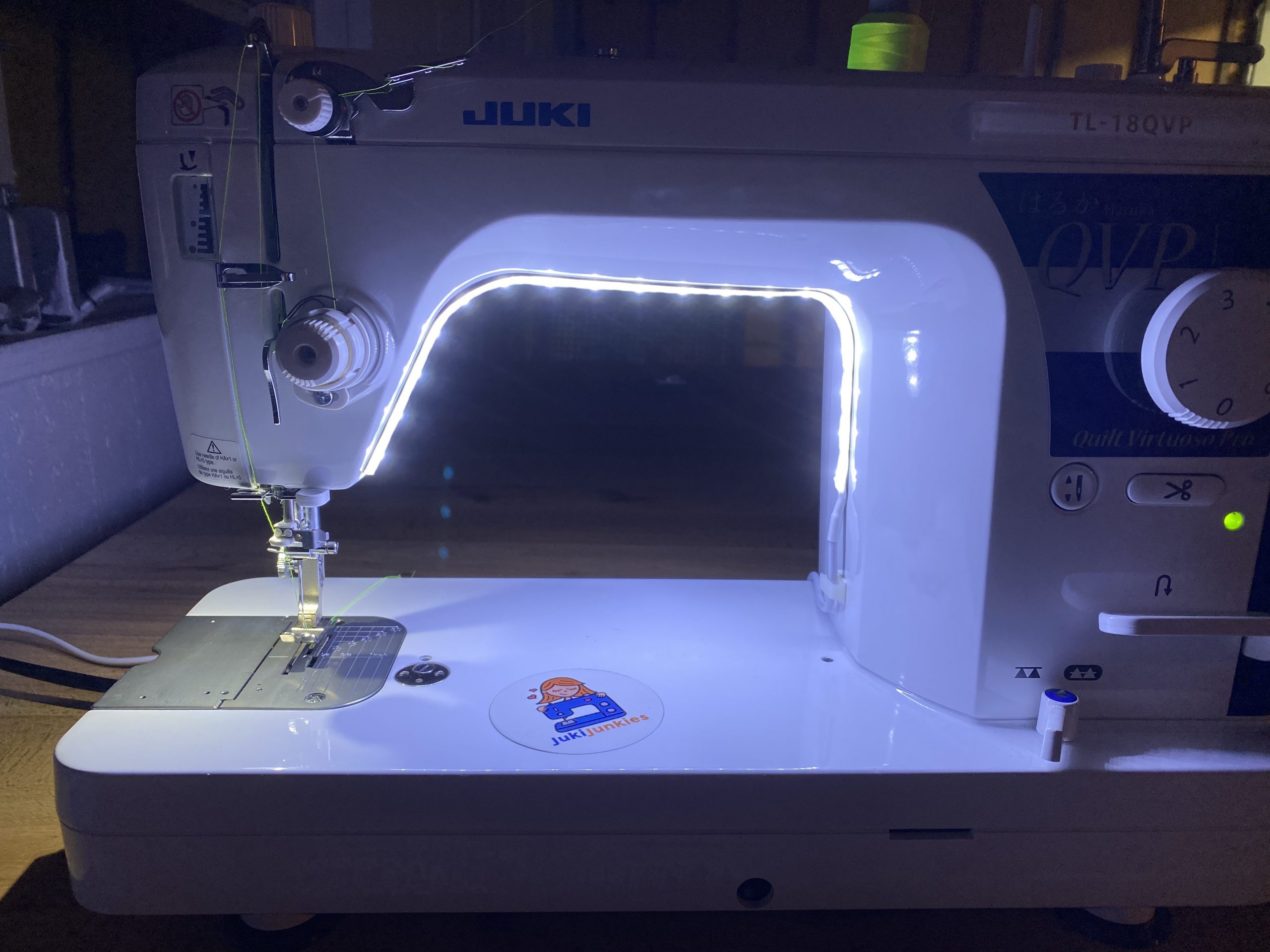
Illustrative Image (Source: Google Search)
Strategic sourcing should also consider regional supply chain capabilities, lead times, and after-sales support to mitigate risks associated with international procurement. Building partnerships with manufacturers who provide clear installation guidance and customization options will empower your operations with enhanced lighting performance and energy efficiency.
Looking ahead, technological advancements in LED dimming controls and smart integration are poised to transform sewing machine illumination. Buyers are encouraged to engage proactively with innovative suppliers and stay informed about emerging trends to maintain a competitive edge. Embrace strategic sourcing not just as a transactional process but as a value-driven partnership that fuels operational excellence and sustainable growth in your textile manufacturing ventures.