Guide to Flicker Led (A Common Strip Issue)
- Introduction: Navigating the Global Market for flicker led (a common strip issue)
- Understanding flicker led (a common strip issue) Types and Variations
- Key Industrial Applications of flicker led (a common strip issue)
- Strategic Material Selection Guide for flicker led (a common strip issue)
- In-depth Look: Manufacturing Processes and Quality Assurance for flicker led (a common strip issue)
- Manufacturing Processes for Flicker-Resistant LED Strips
- Quality Assurance Frameworks and Standards
- Quality Control Checkpoints
- How B2B Buyers Can Verify Supplier Quality Assurance
- Quality Assurance Nuances for Different International Markets
- Conclusion
- Comprehensive Cost and Pricing Analysis for flicker led (a common strip issue) Sourcing
- Spotlight on Potential flicker led (a common strip issue) Manufacturers and Suppliers
- Essential Technical Properties and Trade Terminology for flicker led (a common strip issue)
- Navigating Market Dynamics, Sourcing Trends, and Sustainability in the flicker led (a common strip issue) Sector
- Frequently Asked Questions (FAQs) for B2B Buyers of flicker led (a common strip issue)
- Strategic Sourcing Conclusion and Outlook for flicker led (a common strip issue)
Introduction: Navigating the Global Market for flicker led (a common strip issue)
In today’s interconnected global economy, LED strip lighting stands as a vital component across numerous industries—from commercial infrastructure and hospitality to retail and urban development. However, one persistent technical challenge that can undermine the performance and reliability of these lighting solutions is LED flickering. For B2B buyers operating in diverse markets such as Africa, South America, the Middle East, and Europe, understanding and addressing flicker issues is essential not only to safeguard end-user satisfaction but also to protect brand reputation and reduce costly after-sales service.
This comprehensive guide is designed to empower international buyers with a deep and actionable understanding of flicker phenomena in LED strips—a common yet complex issue. It explores the full spectrum of flicker types, including visible and invisible fluctuations, and dives into the root causes spanning electrical components, power supply compatibility, connection integrity, and environmental influences. Additionally, the guide sheds light on manufacturing standards, quality control practices, and the critical evaluation of supplier capabilities to ensure product consistency and longevity.
Buyers will find detailed insights on cost factors, market trends, and sourcing strategies tailored for regions such as Saudi Arabia and Poland, where varying power grid conditions and installation environments require specialized considerations. Moreover, an extensive FAQ section addresses real-world concerns, enabling procurement teams and project managers to make informed decisions with confidence. By leveraging this resource, international B2B buyers can mitigate flicker-related risks, optimize supply chain choices, and ultimately deliver superior lighting solutions that meet stringent performance expectations across global markets.
Understanding flicker led (a common strip issue) Types and Variations
Type Name | Key Distinguishing Features | Primary B2B Applications | Brief Pros & Cons for Buyers |
---|---|---|---|
Visible Flickering | Flicker frequency below 100 Hz, perceptible to the human eye | Retail, hospitality, office environments | Pros: Immediate visibility aids troubleshooting; Cons: Causes discomfort and health risks for occupants |
Invisible Flickering | Flicker frequency above 100 Hz, imperceptible but present | Industrial, manufacturing, healthcare | Pros: Less noticeable, avoids visual distraction; Cons: Can still cause eye strain and headaches over time |
Dimming Compatibility Flicker | Occurs when dimmer and LED strip/driver protocols mismatch | Architectural lighting, entertainment venues | Pros: Enables lighting control; Cons: Requires careful component matching, risk of flicker if incompatible |
Power Supply Induced Flicker | Flicker due to overloaded, faulty, or low-quality LED drivers | Large-scale installations, commercial projects | Pros: Stable power supply enhances longevity; Cons: Poor supply causes frequent flicker, possible equipment damage |
Connection-Related Flicker | Flicker caused by loose, corroded, or poor solderless connections | Modular lighting setups, temporary installations | Pros: Easy to fix with proper connectors; Cons: Frequent maintenance needed if connectors are low quality |
Visible Flickering
Visible flickering is characterized by a low-frequency pulsation of the LED strip light that can be seen by the naked eye. This type is especially critical in environments where visual comfort and safety are paramount, such as offices, retail spaces, and hospitality venues. For B2B buyers in Africa, South America, the Middle East, and Europe, selecting LED strips and drivers that minimize visible flicker can reduce health-related complaints and improve customer satisfaction. When specifying products, prioritize those with flicker-free certifications and test samples under typical operating conditions.
Invisible Flickering
Invisible flickering occurs at high frequencies beyond human perception but can still cause subtle health effects such as eye strain and headaches. It is common in industrial and healthcare settings where lighting must be consistent yet unobtrusive. Buyers should assess LED driver quality and filtering capabilities to ensure minimal ripple voltage and electromagnetic interference. For regions with unstable power grids, investing in LED products with robust power conditioning features is advisable to mitigate invisible flicker and enhance operational reliability.
Dimming Compatibility Flicker
This flicker type emerges when LED strips, drivers, and dimmers are incompatible or mismatched, often seen in sophisticated architectural lighting or entertainment applications requiring variable light levels. For international B2B buyers, understanding the dimming protocols (e.g., 0-10V, DALI, PWM) and ensuring alignment across all components is essential to prevent flicker. Selecting suppliers that provide comprehensive compatibility documentation and technical support can reduce installation challenges and minimize costly callbacks.
Power Supply Induced Flicker
Power supply-related flickering arises from overloaded, faulty, or low-quality LED drivers unable to maintain stable current delivery. This issue is prevalent in large commercial projects where power demands are high. Buyers should specify power supplies with at least 20% capacity overhead and superior filtering components to reduce ripple voltage. In regions like the Middle East and South America where power quality varies, considering power conditioning units or uninterruptible power supplies (UPS) can protect LED investments and ensure consistent lighting performance.
Connection-Related Flicker
Flickering caused by connection issues stems from loose, corroded, or poorly soldered joints, especially in modular or temporary lighting installations. For B2B buyers managing projects in diverse climates such as Europe or Africa, using high-quality soldered connections rather than solderless connectors reduces flicker risks and maintenance costs. Regular inspection protocols and training for installation teams on best connection practices can further minimize flickering caused by connection failures, enhancing overall system reliability.
Related Video: 7 Common LED Strip FAILS and How To Avoid Them
Key Industrial Applications of flicker led (a common strip issue)
Industry/Sector | Specific Application of flicker led (a common strip issue) | Value/Benefit for the Business | Key Sourcing Considerations for this Application |
---|---|---|---|
Commercial Retail | Ambient and accent lighting in stores and malls | Enhances customer experience by maintaining consistent lighting | Compatibility with dimmers, stable power supply, high-quality LED drivers |
Hospitality & Events | Decorative lighting for hotels, conference centers, and venues | Creates appealing atmospheres without distracting flicker | Robust connectors, flicker-free dimming control, moisture-resistant components |
Industrial Facilities | Task and safety lighting in manufacturing and warehouses | Ensures worker safety and productivity with stable illumination | Durable LED strips with flicker mitigation, power supply capacity, EMI shielding |
Healthcare | Examination and procedure lighting | Prevents eye strain and headaches for staff and patients | High-quality drivers with low ripple, flicker-free performance, regulatory compliance |
Office & Commercial | General and architectural lighting in office buildings | Improves employee comfort and reduces health risks | Reliable power sources, compatibility with building management systems |
Commercial Retail
In retail environments across Africa, South America, the Middle East, and Europe, flicker-free LED strips are essential for creating inviting and visually appealing spaces. Flickering lights can deter customers and reduce time spent in stores, impacting sales. Buyers must prioritize LED strips with compatible dimmers and stable power supplies to avoid flicker caused by voltage fluctuations or mismatched components. Ensuring high-quality drivers and soldered connections will maintain lighting consistency, enhancing brand image and customer satisfaction.
Hospitality & Events
Hotels and event venues demand flawless lighting to set moods and enhance guest experiences. Flickering LED strips can distract attendees and damage reputations. For international B2B buyers in regions like Saudi Arabia and Poland, sourcing moisture-resistant LED strips with robust connectors and flicker-free dimming technology is critical. These features ensure lighting reliability even in humid or variable environments, reducing maintenance costs and ensuring seamless event execution.
Industrial Facilities
Manufacturing plants and warehouses rely heavily on LED strip lighting for safety and operational efficiency. Flickering can cause visual fatigue and increase accident risk. Industrial buyers, especially in power-sensitive regions, should focus on LED strips designed with flicker mitigation technologies, sufficient power supply capacity, and electromagnetic interference (EMI) shielding. Durable construction and quality assurance help maintain consistent illumination in harsh industrial settings, supporting workforce productivity and regulatory compliance.
Healthcare
Medical facilities require stable, flicker-free lighting to prevent eye strain and headaches among healthcare professionals and patients. Flickering lights can compromise diagnostic accuracy and staff well-being. B2B buyers in healthcare sectors across Europe and the Middle East must source LED strips with low ripple drivers, reliable power management, and compliance with medical lighting standards. These specifications ensure safe, comfortable environments critical for patient care and staff performance.
Office & Commercial
In office buildings, flickering LED strips negatively affect employee comfort and productivity, potentially causing headaches and reduced concentration. For commercial real estate buyers in emerging and developed markets, selecting LED strips with reliable power supplies and compatibility with advanced building management systems is paramount. Such lighting solutions promote healthier workspaces, reduce energy costs, and support sustainability initiatives, aligning with corporate social responsibility goals.
Related Video: What is Industrial Automation?
Strategic Material Selection Guide for flicker led (a common strip issue)
Analysis of Common Materials for Flicker LED Strip Components
Selecting the right materials for flicker LED strip components is critical for ensuring stable performance, longevity, and compliance with international standards. B2B buyers from diverse regions such as Africa, South America, the Middle East, and Europe must consider environmental conditions, power quality, and regulatory requirements when choosing materials. Below is an analysis of four common materials used in LED strip manufacturing and assembly, focusing on their impact on flicker issues and overall product reliability.
1. Copper (Cu) for Conductive Traces and Wiring
Key Properties:
Copper is widely used for conductive pathways in LED strips due to its excellent electrical conductivity (~5.96×10^7 S/m), good thermal conductivity, and moderate corrosion resistance when properly coated. It withstands typical operating temperatures of LED strips (up to ~105°C) without significant degradation.
Pros & Cons:
– Pros: Superior electrical conductivity reduces voltage drops and current fluctuations, directly mitigating flicker caused by unstable power delivery. Copper’s thermal conductivity helps dissipate heat, preserving LED chip integrity.
– Cons: Copper is prone to oxidation and corrosion if not adequately protected by coatings like tin or gold plating, especially in humid or salty environments. It also adds to manufacturing complexity and cost compared to aluminum.
Impact on Application:
Copper traces ensure stable current flow, reducing flicker caused by electrical instability. In regions with high humidity or coastal exposure (e.g., parts of South America and the Middle East), corrosion-resistant coatings are essential to maintain performance.
Regional Considerations:
Buyers in Europe (e.g., Poland) and the Middle East (e.g., Saudi Arabia) must ensure compliance with standards such as IEC 60228 (conductors) and RoHS directives limiting hazardous substances. African and South American markets may prioritize cost-effective copper alloys with protective coatings to balance price and durability.
2. Flexible Polyimide (PI) Substrate
Key Properties:
Polyimide films serve as flexible substrates for LED strips, offering excellent thermal stability (up to 260°C), chemical resistance, and mechanical flexibility. PI substrates maintain dimensional stability under thermal cycling, crucial for preventing micro-cracks that cause flicker-inducing intermittent connections.
Pros & Cons:
– Pros: High thermal resistance prevents substrate deformation and delamination, preserving solder joints and electrical continuity. Flexibility allows for versatile installation in curved or irregular surfaces.
– Cons: Higher material and processing costs compared to cheaper PET (polyethylene terephthalate) substrates. Requires specialized manufacturing processes, increasing lead times.
Impact on Application:
PI substrates reduce flicker caused by mechanical stress and thermal fatigue, common in outdoor or industrial installations. Their chemical resistance is beneficial in harsh environments, such as industrial zones in South America or arid regions in the Middle East.
Regional Considerations:
European buyers often demand compliance with REACH and RoHS for substrate materials. In Africa and South America, cost sensitivity may lead to selective use of PI substrates only in high-end or critical applications, balancing performance and budget.
3. Silicone Encapsulation
Key Properties:
Silicone is used to encapsulate LED strips, providing moisture and dust protection while maintaining flexibility. It has excellent UV resistance and operates reliably across a wide temperature range (-50°C to 200°C).
Pros & Cons:
– Pros: Enhances durability by preventing moisture ingress that can cause short circuits and flicker. UV stability is crucial for outdoor installations, preventing yellowing and degradation.
– Cons: Silicone encapsulation adds cost and can complicate recycling. It may also increase the strip’s thickness, limiting use in tight spaces.
Impact on Application:
Silicone encapsulation is vital for flicker prevention in outdoor or humid environments, such as coastal regions in Africa and the Middle East, where moisture and UV exposure are significant concerns.
Regional Considerations:
Buyers in Europe and the Middle East prioritize silicone encapsulated strips for compliance with IP65/IP67 ingress protection standards. In South America, where tropical climates prevail, silicone encapsulation extends product lifespan and reduces maintenance costs.
4. Aluminum Backing/Heat Sink
Key Properties:
Aluminum is commonly used as a backing material or integrated heat sink due to its high thermal conductivity (~205 W/m·K) and lightweight nature. It effectively dissipates heat generated by LED chips, which is crucial for maintaining stable electrical performance and preventing flicker.
Pros & Cons:
– Pros: Efficient heat dissipation reduces thermal stress on LED chips and solder joints, minimizing flicker caused by temperature-induced electrical instability. Aluminum is cost-effective and easy to machine.
– Cons: Aluminum is electrically conductive, requiring careful insulation to prevent shorts. It is susceptible to corrosion without anodizing or protective coatings, especially in humid or salty environments.
Impact on Application:
Aluminum backing is essential for high-power LED strips or installations in warm climates (e.g., Saudi Arabia, northern Africa) to manage heat and maintain flicker-free operation.
Regional Considerations:
European buyers expect compliance with EN 485 standards for aluminum products and may prefer anodized finishes for enhanced corrosion resistance. In South America and Africa, anodized or powder-coated aluminum options balance durability and cost.
Summary Table of Materials for Flicker LED Strip Components
Material | Typical Use Case for flicker led (a common strip issue) | Key Advantage | Key Disadvantage/Limitation | Relative Cost (Low/Med/High) |
---|---|---|---|---|
Copper (Cu) | Conductive traces and wiring for stable current delivery | Excellent electrical and thermal conductivity | Prone to corrosion without protective coatings | Medium |
Flexible Polyimide (PI) | Substrate providing mechanical and thermal stability | High thermal resistance and flexibility | Higher cost and complex manufacturing process | High |
Silicone Encapsulation | Protective coating against moisture and UV for outdoor use | Superior moisture and UV resistance | Adds thickness and cost; complicates recycling | Medium |
Aluminum Backing | Heat sink and backing material for thermal management | Efficient heat dissipation and lightweight | Requires insulation; corrosion risk without treatment | Low to Medium |
This material selection guide enables B2B buyers to make informed decisions tailored to their regional environmental challenges, regulatory requirements, and budget constraints. Prioritizing materials that enhance electrical stability and environmental resilience will significantly reduce flicker issues and improve the reliability of LED strip installations worldwide.
In-depth Look: Manufacturing Processes and Quality Assurance for flicker led (a common strip issue)
Manufacturing Processes for Flicker-Resistant LED Strips
To ensure LED strips exhibit minimal flicker—a common and disruptive issue—manufacturers must follow rigorous and precise production processes. Understanding these steps helps B2B buyers evaluate supplier capabilities and product reliability.
1. Material Preparation
Material selection and preparation are foundational. High-quality LED chips, substrates (usually flexible PCBs), and electronic components (resistors, capacitors, drivers) are sourced from reputable vendors with traceability. Materials undergo incoming quality control (IQC) to verify specifications such as electrical characteristics, thermal resistance, and mechanical durability. For flicker-sensitive applications, components with stable electrical parameters and low tolerance ranges are prioritized.
2. Forming and PCB Fabrication
The flexible printed circuit boards (PCBs) are fabricated using precision photolithography and etching techniques to create circuit pathways. For flicker reduction, the PCB design incorporates optimized trace widths and grounding methods to minimize electrical noise and voltage drops. The copper layers and solder masks are applied under controlled conditions to ensure consistent conductivity and insulation. Automated optical inspection (AOI) often follows this stage to detect manufacturing defects early.
3. Assembly and Soldering
LED chips and passive components are placed on the PCB using high-precision surface mount technology (SMT). For flicker reduction, consistent and reliable solder joints are critical; poor soldering can cause intermittent connections leading to flicker. Reflow soldering ovens with controlled temperature profiles ensure solid joints without component damage. Some manufacturers use gold wire bonding in chip-on-board (COB) LEDs to improve electrical contact reliability, which reduces flickering risks associated with poor chip-to-holder connections.
4. Driver Integration and Encapsulation
The LED driver, a crucial flicker mitigation element, is integrated either on the strip or externally. Drivers with high-quality filtering capacitors and stable current regulation minimize voltage ripple, a primary flicker cause. Encapsulation with silicone or epoxy protects the strip from moisture and mechanical stress, both of which can degrade electrical contacts and induce flicker over time.
5. Finishing and Packaging
Final steps include cutting the LED strips to length, attaching connectors, and packaging with anti-static and moisture barrier materials. Packaging often includes user guidelines on compatible drivers and dimmers to prevent flicker issues stemming from mismatched components.
Quality Assurance Frameworks and Standards
International B2B buyers should demand adherence to stringent quality management and product standards to ensure flicker-free LED strips.
ISO 9001: Quality Management System
Most reputable manufacturers implement ISO 9001 certification, which mandates systematic quality management practices across production. It ensures consistent process control, documentation, and continuous improvement. Buyers can request ISO 9001 certificates to verify the supplier’s commitment to quality.
Product and Safety Certifications
- CE Marking (Europe): Indicates conformity with EU safety, health, and environmental requirements. It covers electrical safety and electromagnetic compatibility—key to flicker reduction.
- RoHS Compliance: Restricts hazardous substances that could affect LED strip longevity and performance.
- UL Certification (North America, recognized globally): Ensures electrical safety and performance standards are met.
- Other regional certifications: For Middle Eastern buyers (e.g., SASO in Saudi Arabia), South America, and African markets, compliance with local electrical and safety standards is critical to avoid customs and operational issues.
Quality Control Checkpoints
Quality control (QC) is embedded at multiple stages to detect and correct issues that could lead to flicker.
Incoming Quality Control (IQC)
Checks raw materials and components for defects, electrical specs, and compatibility. For flicker-sensitive LED strips, IQC verifies LED chip consistency and driver specifications before assembly.
In-Process Quality Control (IPQC)
Continuous monitoring during assembly ensures solder joint integrity, component placement accuracy, and driver integration. Automated optical inspection (AOI) and manual spot checks are common. Real-time electrical testing at this stage can detect early flicker risks due to assembly faults.
Final Quality Control (FQC)
Finished strips undergo comprehensive tests before shipment, including:
- Electrical Tests: Voltage and current stability under various loads.
- Flicker Testing: Using specialized flicker meters or oscilloscopes to measure light output stability and detect visible/invisible flicker frequencies.
- Environmental Stress Testing: Thermal cycling, moisture exposure, and vibration tests to simulate real-world conditions.
- Functional Tests: Compatibility with dimmers and drivers to ensure flicker-free dimming performance.
How B2B Buyers Can Verify Supplier Quality Assurance
Factory Audits and Inspections
International buyers are advised to conduct or commission third-party factory audits to evaluate manufacturing processes, QC protocols, and worker training. Audits can uncover potential flicker risks related to process inconsistencies or substandard materials.
Review of QC Documentation and Test Reports
Request detailed QC documentation, including IQC, IPQC, and FQC reports. Look for flicker measurement data, electrical parameter logs, and failure rate statistics. Transparency in quality reporting is a strong indicator of supplier reliability.
Third-Party Testing and Certification Verification
Engage independent laboratories to test product samples for flicker performance and compliance with international standards. Verification of certifications such as CE, RoHS, and UL through official databases helps avoid counterfeit or substandard products.
Sample Testing and Pilot Runs
Before large orders, conduct sample testing under your facility’s operating conditions. This practical validation helps detect flicker issues caused by local power quality or installation environments.
Quality Assurance Nuances for Different International Markets
Africa and South America
Power grid instability and voltage fluctuations are common challenges that can exacerbate flicker in LED strips. Buyers should prioritize suppliers whose products incorporate advanced driver filtering and surge protection. Local certifications and import regulations vary widely; working with suppliers familiar with these requirements reduces compliance risks.
Middle East (e.g., Saudi Arabia)
The market demands compliance with SASO and GCC electrical standards. High ambient temperatures require LED strips with robust thermal management to prevent flicker caused by overheating. Select suppliers who provide thermal performance data and warranty assurances tailored to harsh climates.
Europe (e.g., Poland)
Europe’s stringent regulatory environment demands full CE compliance and RoHS adherence. Energy efficiency and dimming compatibility are critical. Buyers benefit from suppliers who provide comprehensive flicker testing data aligned with EU standards and offer products compatible with local dimming protocols such as DALI.
Conclusion
For international B2B buyers sourcing LED strips with minimal flicker, scrutinizing the manufacturing processes and quality assurance systems is vital. Prioritizing suppliers with certified quality management, rigorous multi-stage QC, and proven flicker mitigation techniques ensures reliable, high-performance lighting solutions. Coupled with thorough supplier verification through audits, documentation review, and sample testing, buyers can confidently minimize flicker-related risks and enhance end-user satisfaction across diverse global markets.
Related Video: LED Light Making Process | How LED Lights Made Inside Factory | Manufacturing Process
Comprehensive Cost and Pricing Analysis for flicker led (a common strip issue) Sourcing
Understanding the cost and pricing dynamics behind sourcing LED strips prone to flickering issues is crucial for international B2B buyers aiming to optimize procurement and ensure product reliability. Below is a detailed analysis tailored to buyers from Africa, South America, the Middle East, and Europe, focusing on actionable insights for cost management and negotiation.
Key Cost Components in Flicker-Prone LED Strip Production
-
Materials: The primary cost driver includes the LED chips (SMD, CSP, or COB), flexible PCB substrates, soldering materials, connectors, and power drivers. Higher-quality chips and drivers with advanced filtering capacitors reduce flickering risk but increase material costs. Specialized dimmable drivers or custom circuitry also add to expenses.
-
Labor: Skilled labor is essential for precise soldering and quality assembly, especially to prevent flicker caused by poor connections or defective solder joints. Labor costs vary widely by region, affecting overall pricing.
-
Manufacturing Overhead: Includes facility costs, utilities, machinery depreciation, and quality control systems. Overhead reflects the manufacturer’s investment in maintaining consistent production standards to minimize flicker issues.
-
Tooling and Equipment: Custom tooling for LED strip cutting, soldering automation, and testing rigs for flicker detection can be significant. Investment in advanced diagnostic equipment ensures early identification of flicker-prone units.
-
Quality Control (QC): Rigorous QC processes, including electrical testing under various load and dimming scenarios, add to the cost but are vital for reducing flicker-related defects. QC also covers compliance testing for certifications relevant in different international markets.
-
Logistics: Freight, customs duties, and import taxes impact landed cost. Fragile LED strips require careful packaging, potentially increasing shipping costs. International shipments may also face delays affecting inventory turnover.
-
Margin: Suppliers include profit margins that reflect product complexity, brand reputation, and market demand. High reliability LED strips with flicker mitigation features command premium pricing.
Influential Pricing Factors for B2B Buyers
-
Order Volume and Minimum Order Quantities (MOQ): Larger orders typically yield lower unit prices due to economies of scale. MOQ requirements differ by supplier and can impact upfront investment.
-
Specifications and Customization: Custom lengths, color temperatures, dimmable drivers, and integrated flicker suppression circuitry increase unit costs. Buyers should balance customization benefits against price sensitivity.
-
Material Quality and Certifications: LED strips certified for international standards (CE, RoHS, UL) and those using higher-grade LEDs or drivers often cost more but reduce risks of flicker and failure.
-
Supplier Reliability and Location: Established suppliers with proven quality controls may charge premiums but reduce long-term costs related to defects and returns. Sourcing closer to the buyer (e.g., within Europe for Polish buyers) can reduce logistics costs and lead times.
-
Incoterms and Payment Terms: Terms such as FOB, CIF, or DDP impact the final landed cost and risk allocation. Understanding these is essential for accurate cost forecasting and negotiation leverage.
Practical Buyer Tips for Cost-Efficient Sourcing
-
Negotiate on Volume and Payment Terms: Use forecasted volume commitments to negotiate better pricing tiers and more favorable payment schedules, especially when working with suppliers in Asia or Europe.
-
Prioritize Total Cost of Ownership (TCO): Consider warranty terms, product lifespan, and energy efficiency alongside unit price. Flicker-related failures can lead to costly maintenance and replacements.
-
Request Samples and Conduct Independent Testing: Verify flicker performance under actual operating conditions before large-scale purchase. This reduces risk of costly returns and dissatisfaction.
-
Leverage Regional Trade Agreements: Buyers in Africa, South America, the Middle East, and Europe should explore trade agreements that reduce tariffs or import duties on LED lighting products.
-
Factor in After-Sales Support and Technical Assistance: Suppliers offering technical support for installation and troubleshooting flicker issues add value that may justify slightly higher prices.
-
Be Aware of Pricing Fluctuations: Raw material prices (e.g., copper, rare-earth elements for LEDs) and global logistics costs can fluctuate, affecting pricing. Long-term contracts can stabilize costs.
Indicative Pricing Disclaimer
Prices for LED strips susceptible to flickering vary widely depending on the factors above. As a general reference, basic LED strip units may start at approximately $2–$5 per meter, while premium flicker-resistant strips with certified drivers and enhanced QC can range from $7–$15 per meter or higher. These figures should be validated with specific supplier quotes reflecting current market conditions.
By comprehensively evaluating cost structures and pricing influencers, international B2B buyers can strategically source LED strips that minimize flicker issues while optimizing procurement budgets and ensuring product reliability.
Spotlight on Potential flicker led (a common strip issue) Manufacturers and Suppliers
This section offers a look at a few manufacturers active in the ‘flicker led (a common strip issue)’ market. This is a representative sample for illustrative purposes; B2B buyers must conduct their own extensive due diligence before any engagement. Information is synthesized from public sources and general industry knowledge.
Essential Technical Properties and Trade Terminology for flicker led (a common strip issue)
Critical Technical Properties for Flicker LED Solutions
-
Voltage Compatibility (12V/24V DC)
Ensuring the LED strip’s voltage rating matches the power supply is vital. Using a 12V strip with a 24V driver (or vice versa) causes unstable current flow, leading to flickering or premature failure. For B2B buyers, confirming voltage specs upfront prevents costly returns and project delays, especially when sourcing from diverse international suppliers. -
Power Supply Capacity and Quality
The power supply must provide sufficient current with at least a 20% safety margin above the LED strip’s total wattage. Undersized or low-quality drivers often cause flicker due to voltage dips under load. Buyers should prioritize power supplies with reliable filtering components and overload protection to ensure consistent brightness and longer lifespan.
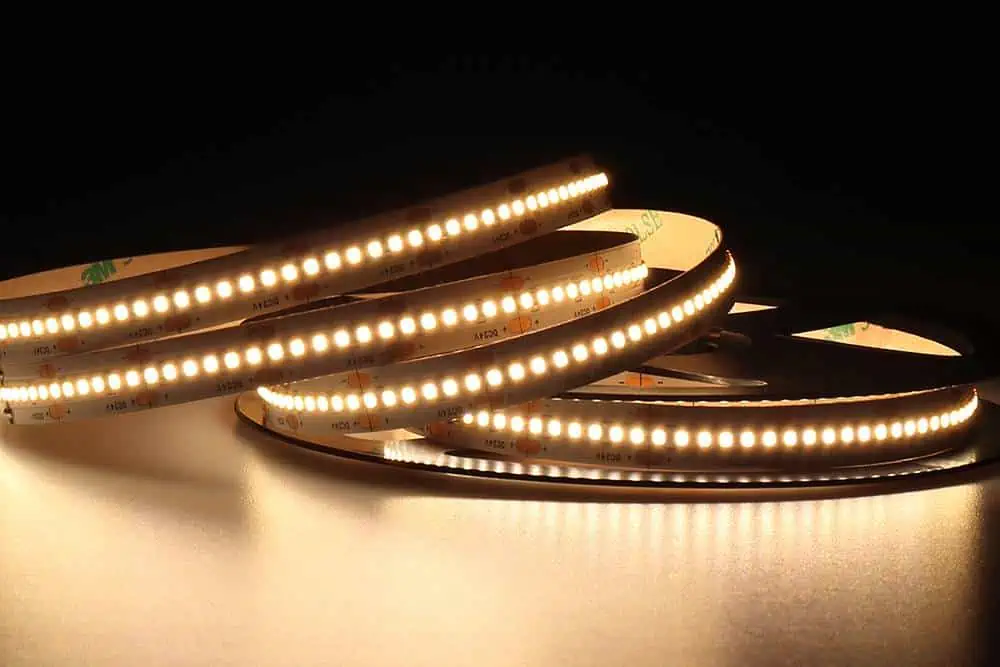
Illustrative Image (Source: Google Search)
-
Dimming Compatibility
LED strips with dimming functions require matched dimmer and driver protocols (e.g., 0-10V, DALI). Mismatched dimming systems cause visible flicker or erratic light output. For projects involving ambiance control or energy savings, specifying dimmer compatibility is crucial to avoid system incompatibility and costly troubleshooting. -
Connection Integrity and Soldering Quality
Flicker often originates from poor or intermittent electrical connections, especially at solderless connectors or poorly soldered joints. Buyers should request products with robust soldering standards and consider recommending soldered connections to clients for critical installations, reducing flicker risk caused by mechanical vibration or corrosion. -
LED Chip and PCB Assembly Quality
The internal construction of LED chips and their attachment to PCBs affects flicker reliability. For example, SMD LEDs connected via fine gold wires are prone to flicker if the wire bond is unstable, whereas CSP or COB LEDs tend to have better stability. B2B buyers must evaluate supplier quality controls to ensure consistent chip-to-PCB bonding and minimize flicker issues. -
Environmental Resistance (IP Rating)
Moisture and dust ingress can cause micro-shorts and flickering in LED strips. Selecting LED strips with appropriate IP ratings (e.g., IP65 or higher for outdoor use) is essential for maintaining performance in harsh environments. Buyers should align IP ratings with installation conditions to prevent flicker caused by environmental factors.
Key Industry Terms for International LED Buyers
-
OEM (Original Equipment Manufacturer)
Refers to a company that manufactures products or components that are purchased by another company and retailed under the purchasing company’s brand. Understanding OEM relationships helps buyers negotiate custom LED strip solutions and ensures product consistency across projects. -
MOQ (Minimum Order Quantity)
The smallest number of units a supplier is willing to sell in one order. MOQ affects pricing and inventory decisions. International buyers, particularly from emerging markets, should negotiate MOQ terms that align with demand forecasts to optimize cash flow and reduce excess stock. -
RFQ (Request for Quotation)
A formal document sent by a buyer to suppliers requesting price and terms for specified products. RFQs facilitate transparent comparisons among multiple suppliers, enabling buyers to secure competitive pricing and favorable delivery terms for LED strips. -
Incoterms (International Commercial Terms)
Standardized trade terms defining responsibilities for shipping, insurance, and tariffs between buyers and sellers in international trade. Common terms include FOB (Free On Board) and CIF (Cost, Insurance, Freight). Buyers must clearly specify Incoterms in contracts to avoid misunderstandings and additional costs during import/export. -
Power Supply Ripple Voltage
The small, rapid fluctuations in DC output voltage from a power supply. Excessive ripple voltage causes LED flickering. Buyers should request technical datasheets specifying ripple voltage limits to ensure driver quality and stable LED performance. -
PWM (Pulse-Width Modulation) Dimming
A dimming method where LED brightness is controlled by rapidly switching the power on and off. Improperly implemented PWM or incompatible drivers can cause flicker visible to the human eye. Buyers should verify dimming technology compatibility to guarantee smooth dimming without flicker.
By mastering these technical properties and trade terms, international B2B buyers can confidently source flicker-free LED strips tailored to diverse market needs, ensuring reliable lighting solutions that enhance client satisfaction and reduce costly after-sales issues.
Navigating Market Dynamics, Sourcing Trends, and Sustainability in the flicker led (a common strip issue) Sector
Market Overview & Key Trends
The global LED strip lighting market has witnessed robust growth fueled by increasing demand for energy-efficient and customizable lighting solutions across commercial, industrial, and residential sectors. However, the persistent issue of flickering LED strips has emerged as a critical concern affecting product reliability, user experience, and operational efficiency. For international B2B buyers—particularly those operating in Africa, South America, the Middle East, and Europe—understanding the market dynamics surrounding flicker-prone LED strips is essential for informed sourcing and project success.
Key Market Drivers:
– Energy Efficiency Mandates: Governments in Europe (e.g., Poland) and the Middle East (e.g., Saudi Arabia) are implementing stricter energy efficiency regulations, increasing adoption of LED strips despite flickering risks.
– Infrastructure Development: Rapid urbanization and infrastructure investments in Africa and South America fuel demand for LED lighting systems, including large-scale architectural and street lighting projects.
– Technological Advancements: The evolution of advanced LED drivers, dimmers, and power supplies that reduce flicker is reshaping supplier capabilities and product portfolios.
Emerging B2B Sourcing Trends:
– Integration of Flicker Mitigation Technologies: Buyers increasingly prioritize LED strips with built-in flicker reduction features such as improved driver electronics and high-quality components to avoid costly retrofits and callbacks.
– Vendor Transparency and Testing: Due to the complexity of flicker causes—ranging from power supply mismatches to connection quality—B2B buyers favor suppliers offering comprehensive testing data and certifications ensuring flicker-free performance.
– Modular and Customizable Solutions: Demand for LED strips adaptable to specific environmental and electrical conditions encourages sourcing from manufacturers who provide modular designs and tailored driver compatibility.
Market Dynamics and Challenges:
– Supply Chain Fragmentation: Sourcing high-quality flicker-resistant LED strips involves navigating a fragmented supplier landscape, especially in emerging markets where product quality varies widely.
– Power Quality Variability: Regions such as parts of Africa and South America experience grid instability, making flicker issues more prevalent and requiring power conditioning solutions integrated with LED systems.
– Cost vs. Quality Trade-offs: While premium flicker-free LED strips command higher upfront costs, buyers must balance initial investments against long-term operational savings and brand reputation risks.
For B2B buyers from Saudi Arabia, Poland, and similar markets, partnering with suppliers who understand local electrical infrastructure and offer robust flicker diagnostics can be a decisive competitive advantage.
Sustainability & Ethical Sourcing in B2B
Sustainability considerations are increasingly influencing procurement decisions in the LED strip lighting sector, driven by global environmental concerns and evolving regulatory frameworks. Flickering LED strips not only compromise performance but may also indicate inefficient energy use and premature product failure, counteracting sustainability goals.
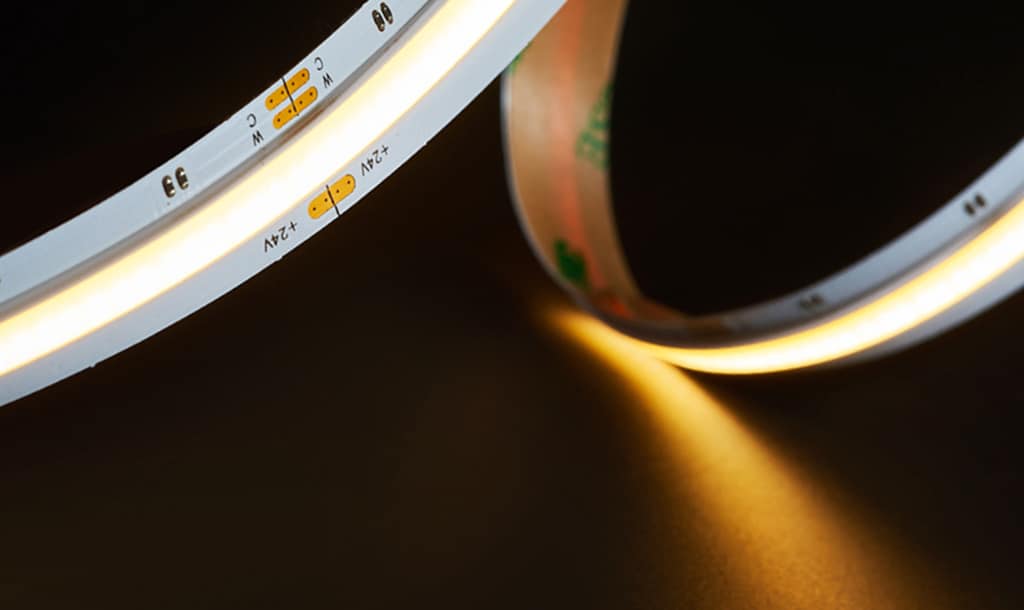
Illustrative Image (Source: Google Search)
Environmental Impact:
– LED strips that flicker often suffer from unstable power consumption patterns, leading to energy waste and higher greenhouse gas emissions over their lifecycle. Replacing faulty or flickering strips more frequently exacerbates electronic waste generation.
– The production of LED components involves rare earth elements and hazardous materials, emphasizing the need for responsible sourcing to minimize ecological footprints.
Ethical Supply Chains:
– B2B buyers must prioritize suppliers committed to transparency, fair labor practices, and conflict-free sourcing of raw materials. This is particularly relevant for African markets where mineral sourcing can be contentious.
– Certifications such as RoHS (Restriction of Hazardous Substances), REACH (Registration, Evaluation, Authorization, and Restriction of Chemicals), and ISO 14001 environmental management standards serve as benchmarks for sustainable and ethical manufacturing practices.
Green Certifications and Materials:
– LED strips incorporating eco-friendly materials—such as lead-free solder, recyclable PCBs, and low-VOC adhesives—are gaining traction among environmentally conscious buyers.
– Certification programs like ENERGY STAR and TUV Rheinland’s quality and safety marks provide assurance that products meet stringent energy efficiency and sustainability criteria, reducing the risk of flicker-related energy inefficiencies.
– Investing in LED drivers with advanced filtering and power conditioning capabilities not only mitigates flicker but also enhances energy savings, aligning with corporate sustainability mandates.
For B2B buyers across Europe, the Middle East, Africa, and South America, embedding sustainability into sourcing strategies for flicker-free LED strips fosters compliance, brand integrity, and long-term cost efficiencies.
Evolution of Flicker LED Strip Technology
The issue of flickering in LED strip lighting traces back to the early adoption of LED technology when power supply and driver electronics were relatively rudimentary. Initially, LED strips were powered by basic drivers that lacked sophisticated current regulation, leading to frequent flicker caused by voltage fluctuations and incompatible dimming controls.
Over time, the industry has seen significant technological advancements:
– The introduction of high-quality constant current drivers and PWM (Pulse Width Modulation) dimming protocols tailored for LEDs improved flicker control.
– Transition from traditional 0-10V dimmers to digital protocols like DALI (Digital Addressable Lighting Interface) enhanced compatibility and reduced flicker incidents.
– Development of CSP (Chip Scale Package) and COB (Chip on Board) LEDs, which eliminate fragile gold wire connections, has improved LED strip reliability and flicker resistance.
Today, the LED strip lighting sector continues to evolve with a focus on integrating intelligent drivers, superior connectivity solutions, and enhanced power supply designs to address flicker challenges comprehensively. For B2B buyers, understanding this evolution is key to selecting future-proof products that align with project requirements and sustainability targets.
Related Video: Global Trade & Logistics – What is Global Trade?
Frequently Asked Questions (FAQs) for B2B Buyers of flicker led (a common strip issue)
-
How can I effectively vet LED strip suppliers to minimize flickering issues?
Thorough supplier vetting is crucial to avoid flickering problems. Request detailed product datasheets, including driver compatibility and dimming protocols. Verify if the supplier conducts rigorous quality control testing, such as voltage stability and flicker frequency analysis. Seek references or case studies from clients in similar markets (e.g., industrial or commercial lighting in Africa or Europe). Additionally, inspect certifications like CE, RoHS, and UL, which indicate adherence to safety and performance standards. Finally, consider suppliers offering samples or pilot orders to test the LED strips under your specific conditions before full-scale procurement. -
What customization options should I prioritize to prevent flickering in LED strip installations?
Customization is key to ensuring compatibility and performance. Prioritize LED strips tailored to your power supply specifications, such as voltage and current ratings, and ensure the dimming system (0-10V, DALI, PWM) matches the driver and controller protocols. For regions with unstable power grids (common in parts of Africa and South America), request enhanced filtering components or integrated surge protection. Specify environmental requirements, like IP ratings for moisture resistance, to avoid flickering caused by circuit shorts. Collaborate with suppliers who can adjust PCB thickness, soldering quality, and chip types (e.g., CSP or COB) to reduce internal flicker risks. -
What are typical minimum order quantities (MOQs) and lead times for flicker-free LED strip orders, and how can I negotiate better terms?
MOQs vary widely but typically range from 500 to 1,000 meters for standard LED strips. Custom or high-spec flicker-free models may have higher MOQs due to specialized components. Lead times generally span 4 to 8 weeks, factoring in production and quality testing. To negotiate better terms, consolidate your order volume by partnering with other buyers or committing to multiple purchase cycles. Emphasize long-term relationships and ask suppliers for staggered delivery schedules or sample batches. Clarify payment terms upfront—many reputable suppliers accept 30% deposits and balance upon shipment to reduce risk. -
Which quality assurance certifications and testing protocols should I require to ensure flicker-free LED strip products?
Demand internationally recognized certifications such as CE (Europe), UL (North America), RoHS (environmental safety), and IEC standards for electrical safety. Additionally, inquire if suppliers perform flicker-specific testing, such as flicker index measurement and ripple voltage assessments using oscilloscopes. Certifications like LM-80 or TM-21 for LED chip longevity and lumen maintenance are also valuable. For buyers in the Middle East or Africa, ensure compliance with local regulations, such as SASO in Saudi Arabia. Finally, request documentation of batch testing results and factory audits to verify consistent production quality. -
How should I plan logistics and shipping to protect sensitive LED strips from damage that could cause flickering?
LED strips are sensitive to electrostatic discharge (ESD), moisture, and mechanical stress. Insist on ESD-safe packaging with anti-static bags and moisture barrier films, particularly for coastal or humid regions like parts of South America or the Middle East. Opt for climate-controlled transport if possible, especially for large shipments. Use reputable freight forwarders experienced in handling electronics and ensure clear labeling for fragile handling. Consider insurance options covering transit damage. Communicate with your supplier about packaging standards and request photos or videos of packed shipments to confirm compliance. -
What payment methods are safest for international B2B transactions involving LED strips prone to flicker issues?
Secure payment methods protect both parties. Letters of Credit (LC) are widely used for international B2B deals, offering assurance that funds are only released upon meeting shipment and quality conditions. Escrow services or trade platforms with milestone payments can also mitigate risks. For trusted partners, Telegraphic Transfers (T/T) with partial upfront payment and balance after inspection are common. Avoid full prepayment without verified supplier credibility. Always link payments to clear contractual terms specifying quality standards, inspection rights, and remedies for flickering defects. -
How can I handle disputes related to flickering LED strip quality or performance with overseas suppliers?
Prevent disputes by incorporating detailed technical specifications, acceptance criteria, and warranty terms in your contract. If flickering occurs, document the issue thoroughly with videos, test reports, and expert assessments. Engage your supplier promptly and seek amicable solutions such as replacement shipments or partial refunds. Utilize third-party inspection agencies or arbitration services specializing in international trade if negotiations stall. Maintain clear communication channels and cultural sensitivity. For buyers in regulated markets like Europe or Saudi Arabia, leverage local trade bodies or chambers of commerce for mediation support. -
Are there regional considerations for flicker LED strip sourcing that B2B buyers in Africa, South America, the Middle East, or Europe should keep in mind?
Absolutely. Power grid stability varies significantly; Africa and parts of South America often experience voltage fluctuations requiring robust filtering and surge protection in LED strips. Middle Eastern buyers should verify compliance with regional certification requirements (e.g., SASO) and consider climate factors like extreme heat. European buyers must prioritize strict CE and RoHS compliance and may benefit from suppliers offering advanced dimming compatibility for smart building integration. Understanding these regional nuances helps tailor your specifications, minimizes flickering risks, and ensures smoother customs clearance and market acceptance.
Strategic Sourcing Conclusion and Outlook for flicker led (a common strip issue)
Effective management of flickering LED strip issues is essential for maintaining product quality, client satisfaction, and operational efficiency in the lighting industry. For international B2B buyers across Africa, South America, the Middle East, and Europe, understanding the technical nuances—such as power supply compatibility, connection integrity, and component quality—enables more informed procurement decisions and reduces costly after-sales service. Strategic sourcing should prioritize suppliers who demonstrate robust quality control, offer compatible dimming and driver solutions, and provide comprehensive technical support.
Key takeaways include:
- Ensuring power supplies exceed the LED strip’s load requirements with adequate filtering to prevent flicker.
- Verifying compatibility among dimmers, drivers, and LED strips to avoid mismatched components.
- Prioritizing reliable connection methods, such as soldered joints over solderless connectors, to minimize intermittent flicker.
- Selecting LED technologies (e.g., CSP or COB) that inherently reduce flicker risks due to superior internal construction.
Looking ahead, buyers should engage with innovative manufacturers emphasizing advanced driver technology and environmental resilience, particularly in regions with variable power quality. Establishing strategic partnerships with trusted suppliers will not only mitigate flickering issues but also drive long-term sustainability and competitiveness in the dynamic global lighting market. Act now by integrating these insights into your sourcing strategy to illuminate your projects with confidence and reliability.